ETEK Parking has implemented a 2-level smart puzzle parking system at the Phu Dong Sky Garden project, effectively solving the challenge of limited parking space.
Packaging line for soft drinks 48.000 units/hour
The soft drink manufacturing plant has built a packaging line to increase production output with twist conveyance technology for the first time introduced in Vietnam.
Our client is a beverage manufacturing plant providing a variety of product lines to the consumer market in Vietnam. These products are available in various outlets ranging from supermarkets, shopping centers to convenience stores, retail outlets in all 64 provinces and cities. The brand holds up to 35% market share with 2 manufacturing plants directly in Vietnam. After the Covid pandemic, the soft drink market became fiercely competitive, bringing challenges that created pressure and motivation for the plant to adapt. ETEK provides an automated packaging line solution for the client's plant.
The production line consists of many different stages, creating demands for corresponding automated machines. The combination of production modules includes:
During the mass project implementation, challenges arise due to the new twist technology, requiring repairs, improvements, and upgrades to ensure smooth production line operation. Despite careful planning in the design phase, during project implementation, ETEK engineers still face various challenges:
Issues Facing the Beverage Manufacturing Plant
Product Output
Post-Covid, despite economic difficulties, there was a significant increase in consumer goods consumption and beverage production. Therefore, the plant's urgent need for product output became a top priority to serve sales and dominate the market. Additionally, there is a need for diverse product lines as well as trends favoring safety and health for consumers.Aesthetic Requirements
Continuous competition drives changes and adaptations for the beverage manufacturing plant to develop. This includes both imported products from Japan, South Korea, Thailand, etc., and domestically produced items. Combining various factors, the plant needs to change both the quality and aesthetics of the products. Packaging, labels, designs, varieties, flavors of the product lines need to be professional, consistent, and increasingly attractive.Product Quality
Product quality is always a top priority to attract savvy customers. Just one defective product released into the market can significantly impact the company's reputation, value, and profits. Therefore, ensuring product quality control is an ongoing challenge that the plant needs to continuously improve.Digitization of the Beverage Manufacturing Plant
The digitization of the plant is a common policy pursued by countries, including Vietnam. Our client is a leading company in the trend towards automation and digitization of manufacturing plants in the soft drink industry.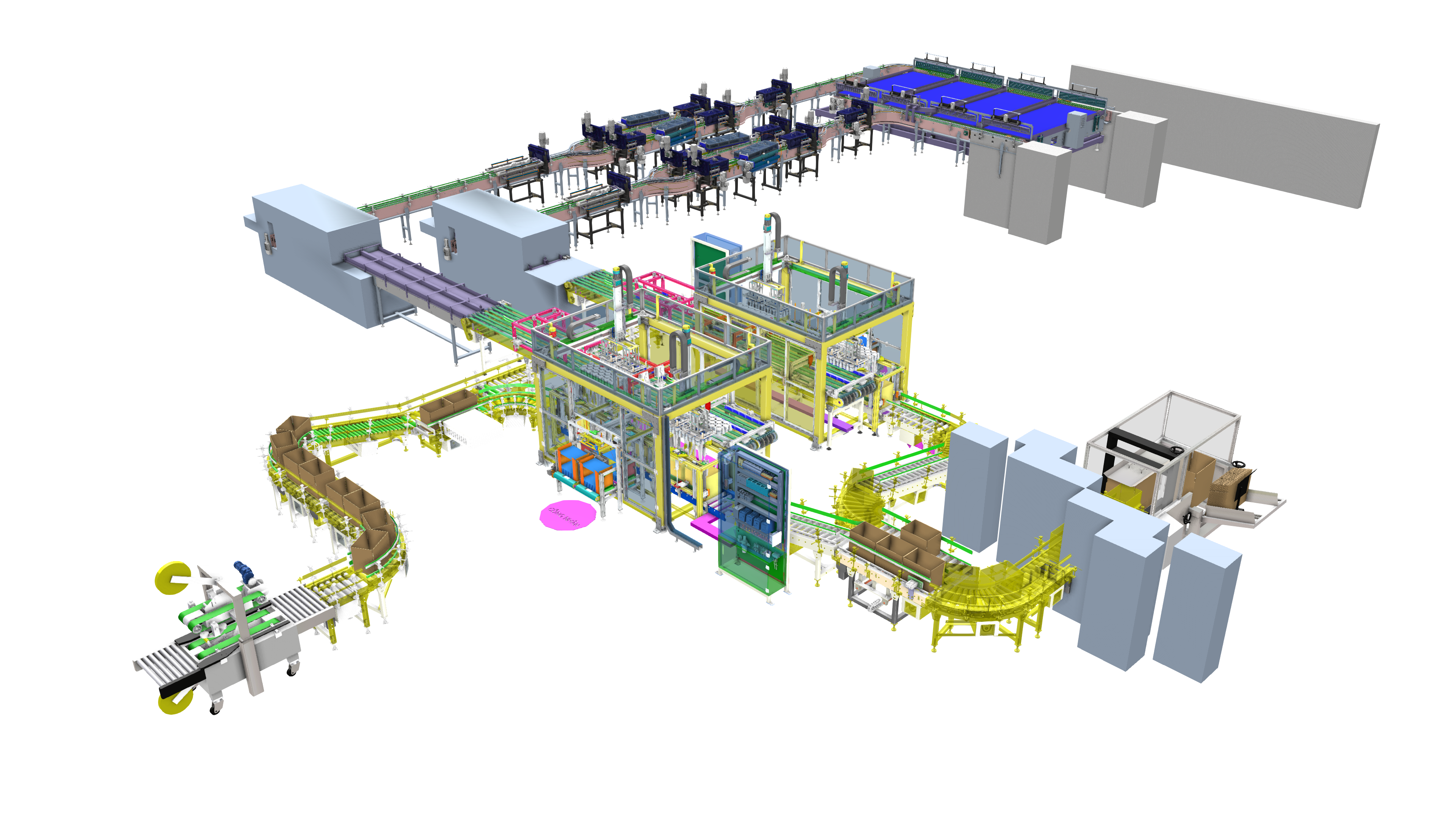
Requirements of the Beverage Manufacturing Plant
Automation
- The plant is currently using 100% manual labor for sorting and packaging bottled soft drinks. Some issues the plant is facing include:
- Increased production volume with insufficient labor.
- Overtime to meet production demands leading to fatigue and lack of focus among workers.
- Diverse packaging methods leading to errors when executed manually.
- Ensuring food safety and hygiene standards in soft drink production.

Technology
- In the path to constructing a modern 4.0 plant, automating the beverage production line is both the first and most crucial step. The plant's requirements for implementing and executing digitization include:
- Connecting production lines.
- Transmitting work signals.
- Quality monitoring.
- Process supervision.
Soft Drink Production Efficiency
As mentioned earlier, the main issue facing the plant is increasing product output. Hence, the plant's firm requirement is to meet production targets.Challenges
Total Line Contractor
Developing a comprehensive automation solution for the beverage production and packaging line sorting process. ETEK identifies this as a crucial project that receives special attention from the client in terms of scale and project value.The production line consists of many different stages, creating demands for corresponding automated machines. The combination of production modules includes:
- Product conveyor belt.
- Twist lane divider/design.
- Twist cup flipping/design.
- Twist lane merging/design.
- Twist block formation/design.
- Heat shrink wrapping machine/standard machine.
- Case packer/grab and stack machine design.
- Straw dispenser machine/standard machine.
- Crate assembly machine/standard machine.
- Crate sealing machine/standard machine.

Technology
- The twist technology is applied to beverage production to meet product sorting specifically for our client's needs. It is created through four distinct stages: lane division, cup flipping, lane merging, and block formation. This technology is developed to shape the product configurations as per the client's requirements.
- The twist technology, although existing globally, is being applied for the first time in Vietnam's market. This presents a significant challenge to ETEK engineers.
- Absorbing technological knowledge poses a significant challenge, given that this is the first time and ETEK is the only unit to introduce this technology into the production line. All research and learning processes are intensive, involving rapid work and experience gathering by ETEK engineers.
- Through real-world simulation software design, ETEK experts have programmed the production line operation. However, the operation process of the production line is a simulation process, requiring independent structure design tailored for this client.
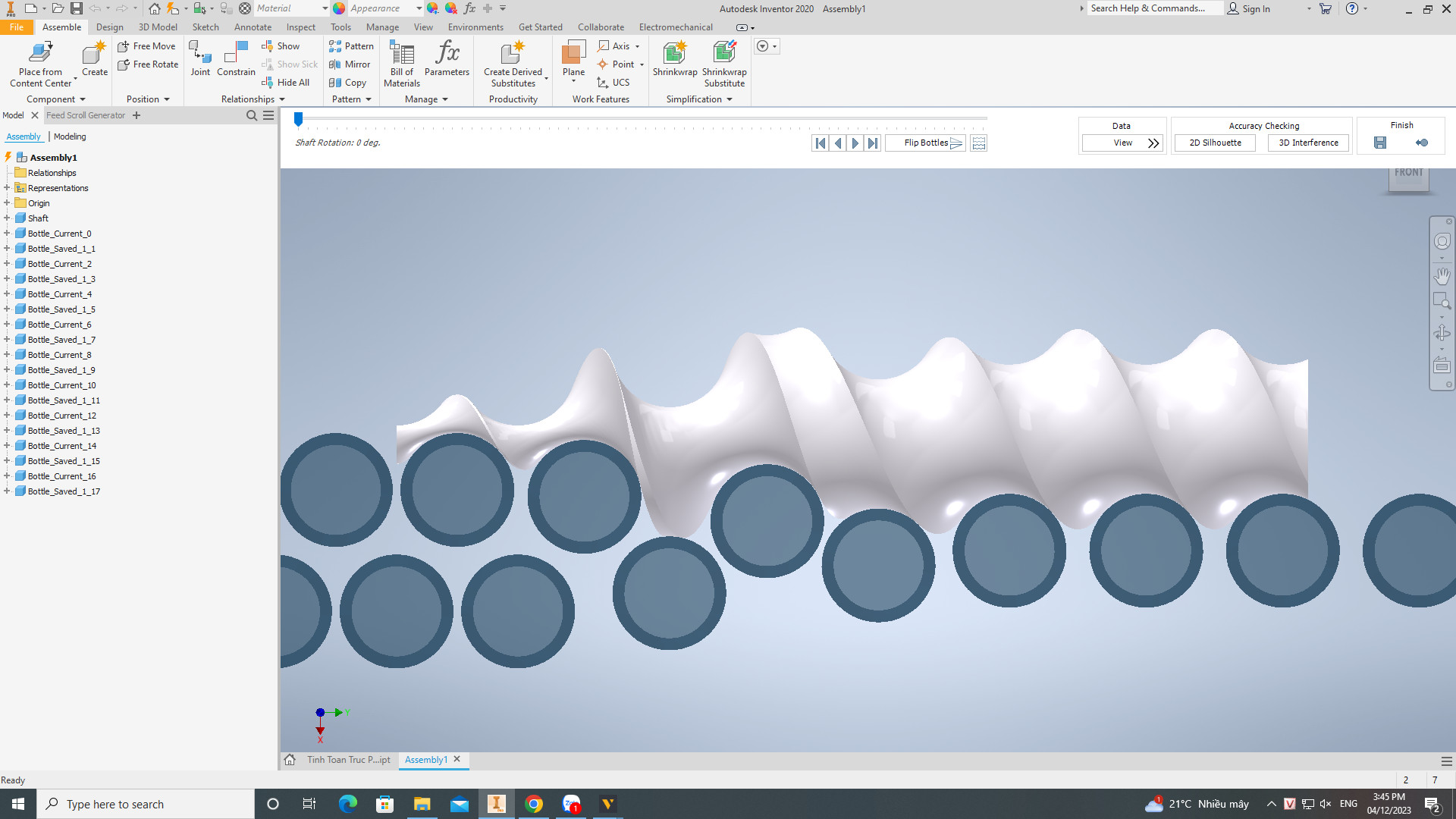
Time
From the client's request to presenting the solution, there is only a 4-week working period. All phases, including technology research, capacity calculations, equipment preparation, and overall solution development, must be simultaneously implemented to meet the deadline.Implementation
The new twist technology requires high-speed and precise beverage production, but during the product testing phase, there is a lack of equipment for trial operation. Precision machining of equipment clusters takes a long time, making trial runs difficult.During the mass project implementation, challenges arise due to the new twist technology, requiring repairs, improvements, and upgrades to ensure smooth production line operation. Despite careful planning in the design phase, during project implementation, ETEK engineers still face various challenges:
- Lane division twist:
- High conveyor belt speed leads to a large number of cups entering, combined with the liquid nature of soft drink cups, causing deviations on the conveyor belt.
- The twist shaft design with a twin-screw input on both sides creates a small input shape, causing "cutting" into the cup, damaging the product.
- The two conveyor belt interface is jammed due to the high entry speed of the cups.
- Block formation twist:
- Liquid cups prone to deformation create gaps, leading to block deviation if cups deform from 4 cups/block to 5 cups/block.
- Cups laid flat to be pressed upwards cause cup spills.
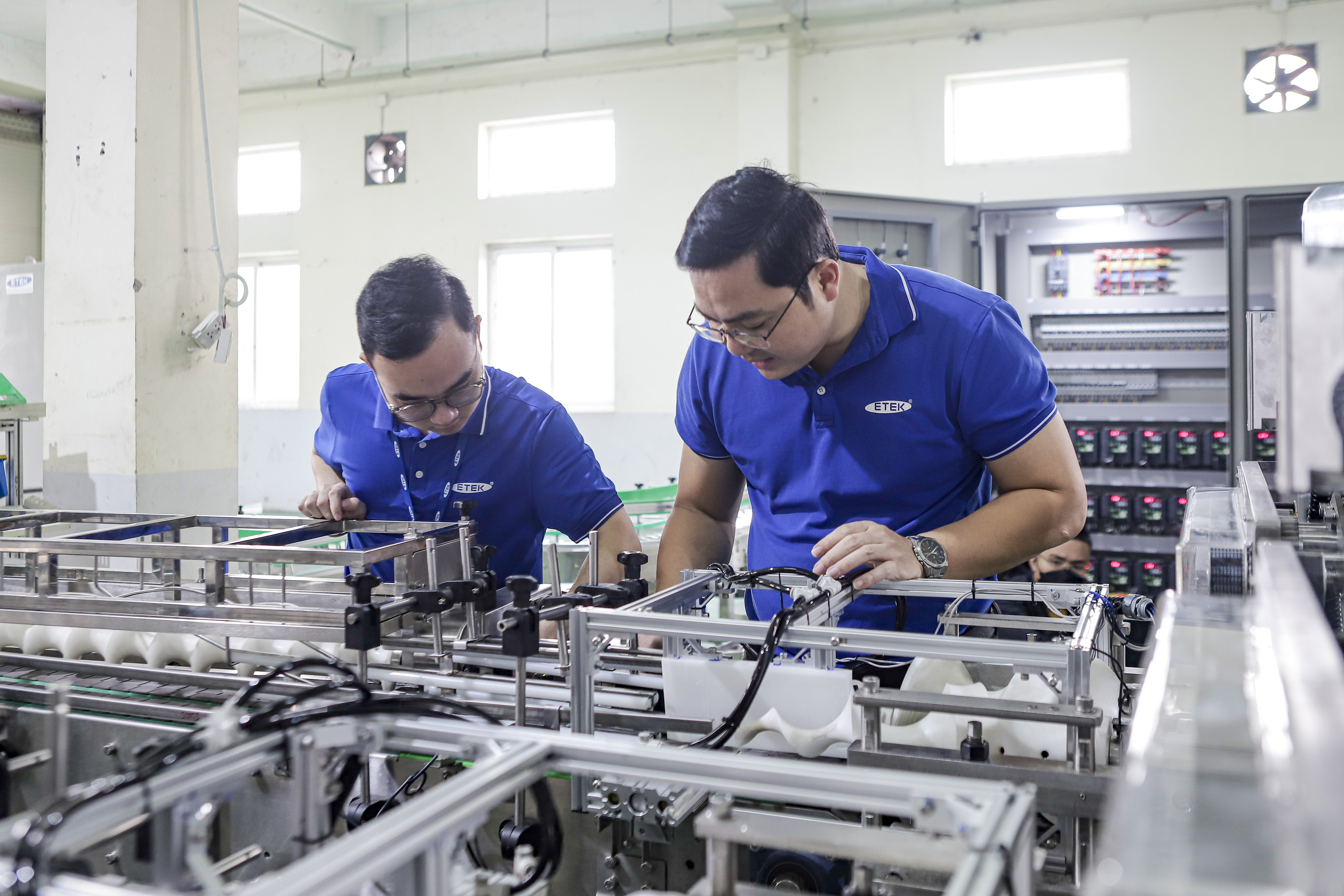
ETEK Solutions
Speed Key
ETEK confidently provides a solution for beverage production efficiency, meeting the client's requirement of 48,000 products/hour. Our engineers utilize realistic simulation software technologies, providing trust and ensuring the client's project success.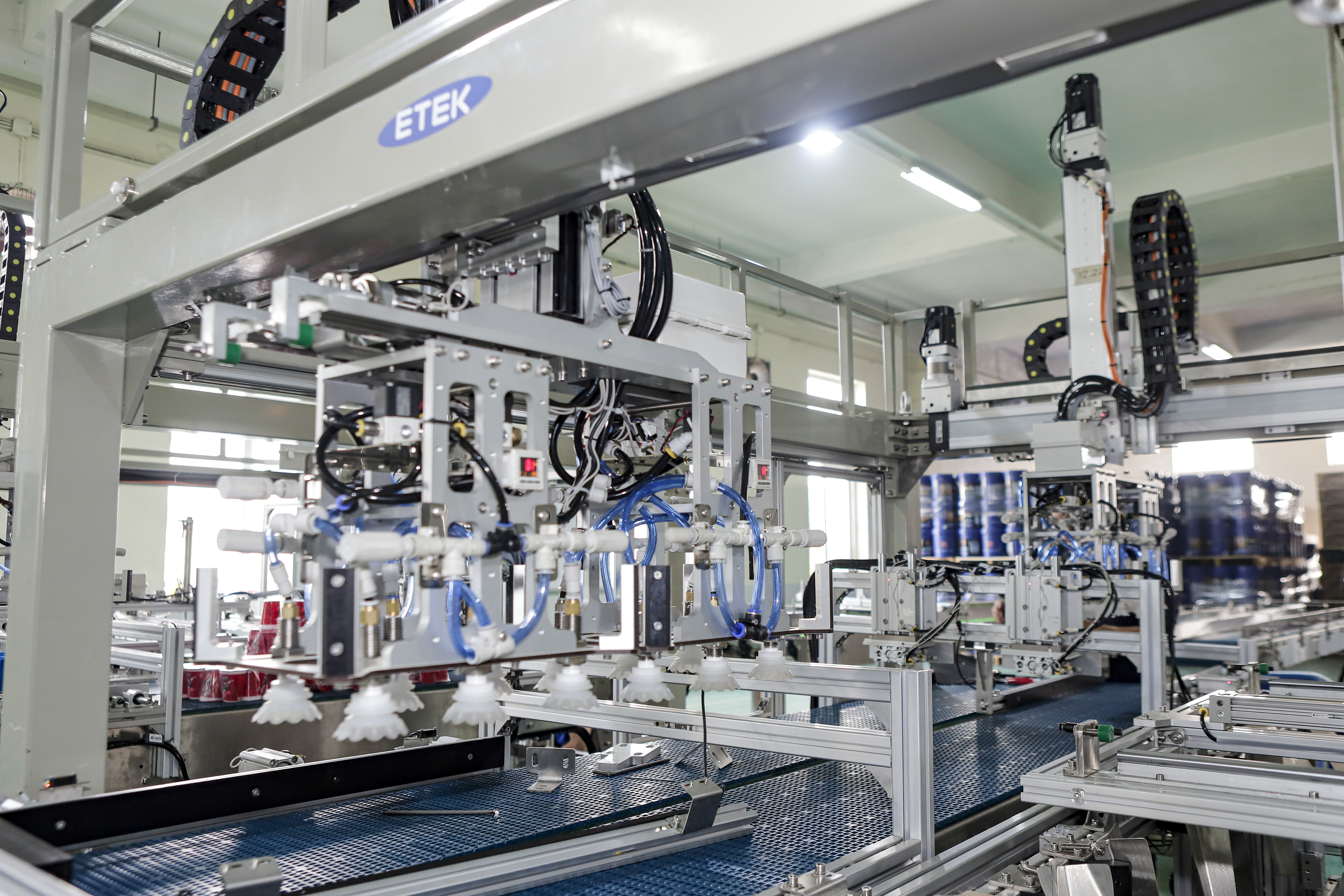
Cost Reduction in Soft Drink Production
The plant invests in a production line to reduce the cost structure of products, thereby increasing competitiveness. The production line increases output, thereby reducing labor costs, excess materials, electricity, etc., meeting the plant's requirements.Safety and Hygiene
The automated production line ensures 100% safety and hygiene standards in beverage production. Additionally, the machinery helps increase the 5S environment in the workplace.Beverage Production Automation
The practical benefits include productivity gains, production monitoring, production line automation, and minimizing errors. Thus, the client and the plant build digitization goals as previously set.Why Choose ETEK
- ETEK is a leading provider of comprehensive automation solutions for beverage production and packaging in Vietnam.
- ETEK provides top-notch technology solutions in the packaging industry for prominent clients like Unilever, Vinfast, P&G, etc.
- ETEK has a team of experienced design engineers, simultaneously implementing multiple large projects.
Benefits Achieved
- Increased productivity by 125%.
- Reduced costs by 4-8%.
- Minimized errors to less than 3%.
- Hygiene standards exceed 99%.
- Plant digitization exceeds 60%.
Others Projects
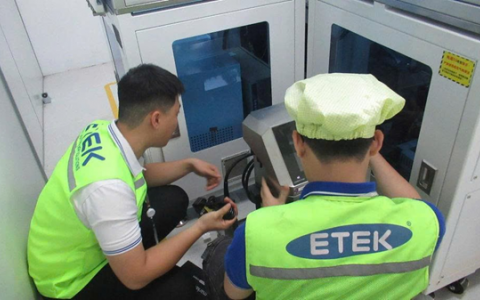
ETEK has successfully implemented a project to supply and install 5 Markem-Imaje 9750+ industrial inkjet printers for an electronic components factory. The project's goal is to replace old printing equipment and meet the increasing requirements for resolution and accuracy in printing micro QR codes on electronic products.

ETEK implemented the Pick to Light system for 15 Kitting areas and 7 Sequencing areas with a total of 3,575 components, reducing picking time, reducing errors and increasing productivity. The project included mechanical and electrical installation, integration with the manufacturing management system (MES) and operator training. The result: increased operational efficiency, synchronized data management, stable operation, meeting the high requirements of the automotive industry.
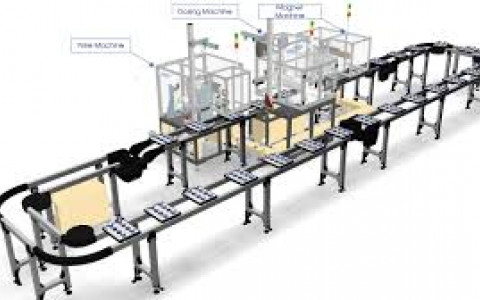
Client: A Japanese enterprise specializing in the production of auxiliary equipment for automobiles and motorcycles
Quantity: 01 assembly line
Project Name: Supply of Speaker Assembly Line
Quantity: 01 assembly line
Project Name: Supply of Speaker Assembly Line
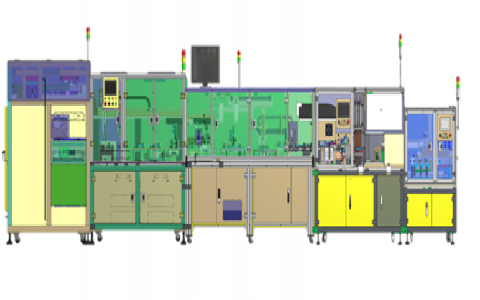
Through nearly 15 years of cooperation and continuous learning from our Customers, ETEK has matured significantly in technical capability and has also achieved comprehensive improvement in processes, management mindset, and working culture. From the early, challenging projects to now, ETEK is honored to be a supplier of numerous machines and production lines, providing various specialized automation equipment for key stages in the industrial manufacturing process.
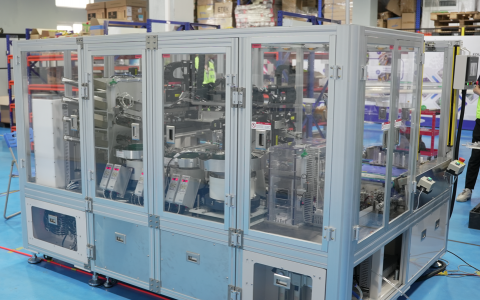
With the orientation of "long-term development with customers, built on technical expertise and sustainable responsibility," we are proud to continue our collaboration with a leading Japanese electronics partner on the Paper Roll Assembly Machine project – a challenging endeavor that stands as a testament to the trust and strong bond between our two companies
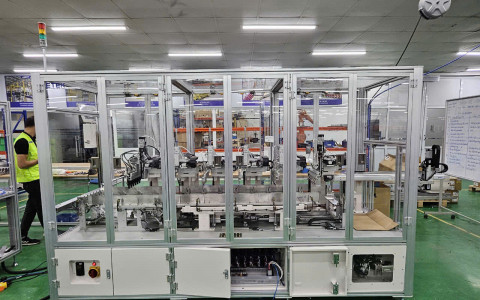
Client: A sports eyewear manufacturing company in China
Quantity: 01 machine
Machine Name: Anti-Fog Coating Machine for Swimming Goggles
Quantity: 01 machine
Machine Name: Anti-Fog Coating Machine for Swimming Goggles
_cr_480x300.png)
ETEK implemented an AGV (Automated Guided Vehicle) system for an automotive manufacturing and assembly plant, aiming to fully automate the transportation of materials, pallets, and trolleys throughout the production line.
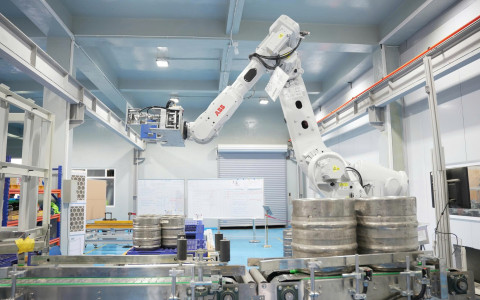
ETEK's automated palletizer system for 30L KEGs boosts production capacity to 400 KEGs/hour, minimizes manual labor, optimizes the process, and ensures stable, 24/7 operation with flexible settings for operational adjustments.
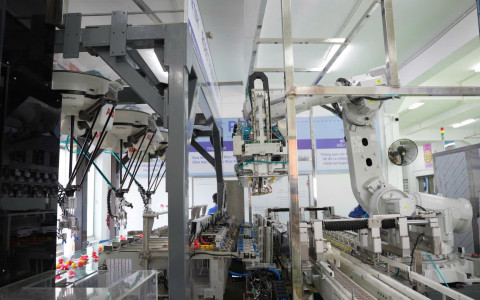
ETEK's automated pump cap tightening line boosts production speed, ensures consistent quality, and reduces operational costs while enhancing real-time defect detection and product removal during the production process.
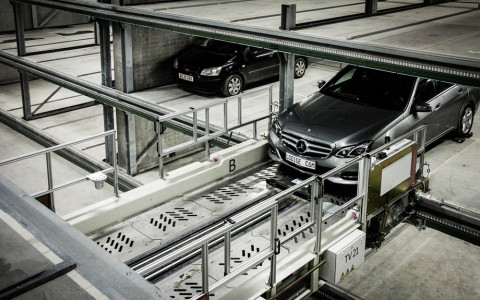
The automatic parking system maximizes the use of space across 3 underground levels, increasing parking capacity compared to traditional lots.
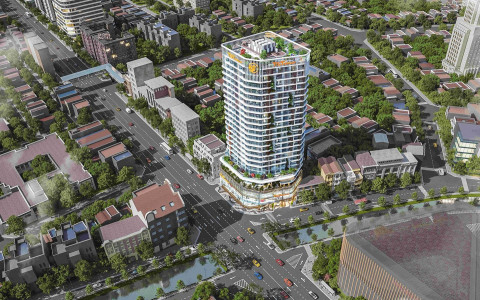
A semi-automatic parking system was deployed throughout all four basement levels, featuring a 2-level puzzle parking solution in each designated basement zone
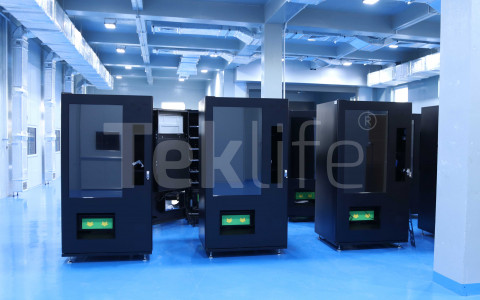
This model of automated product sampling serves not only as an innovative distribution channel, but also as a promising source of revenue for individual investors and product distributors.
_cr_480x300.png)
Case Study: ETEK Implements an Automated Production Line Training Solution at Thai Nguyen University of Technology
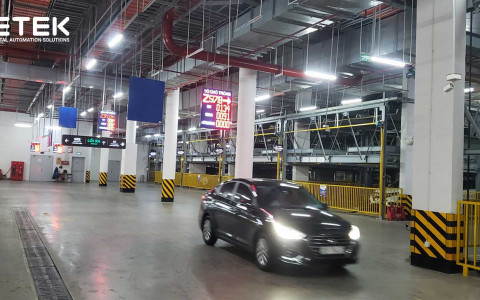
The semi-automatic 3-level puzzle parking system combined with a 2-level motorbike lift is an optimal parking model in terms of space utilization, operational efficiency, and cost-effectiveness.
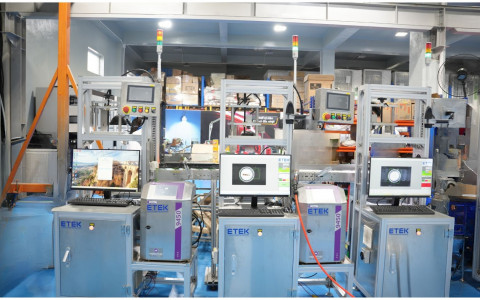
Our client is one of the leading corporations in the food and beverage industry, operating a high-capacity potato snack production line. To ensure product quality and meet the growing market demand, the client set strict requirements for the quality inspection system. ETEK successfully developed and implemented an automated solution for date printing and product quality inspection for the snack production line.
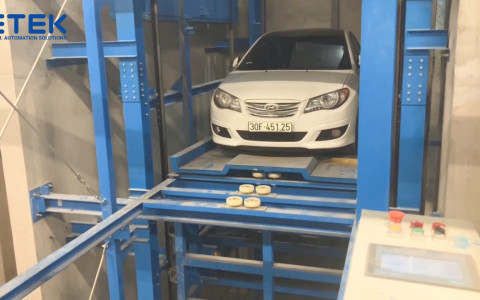
ETEK Parking has successfully implemented an automated parking system using Robocar technology in Quang Ninh – one of the most advanced technologies currently available in the field of automated parking.
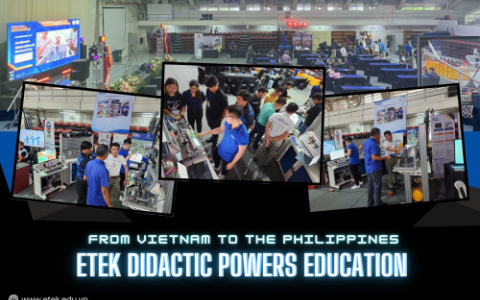
Case Study: From Vietnam to the Philippines – Delivering a Comprehensive Refrigeration Training Solution
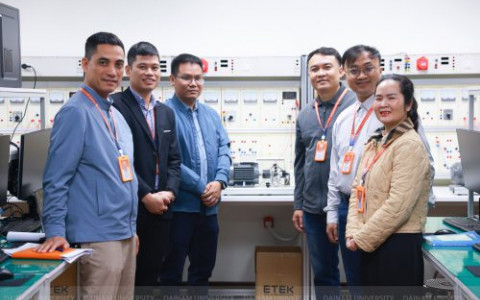
Case Study: ETEK Provides Technical Training Equipment for Dai Nam University
A Modern Training Solution with the Power Electronics Application Training Kit
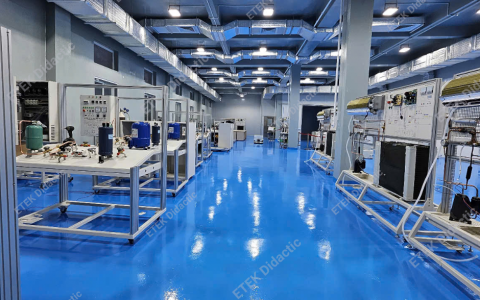
Case Study: ETEK Equips Vietnam Vocational College Korea Ha Noi City with Advanced Training Equipment
Client: Vietnam – Korea Vocational College
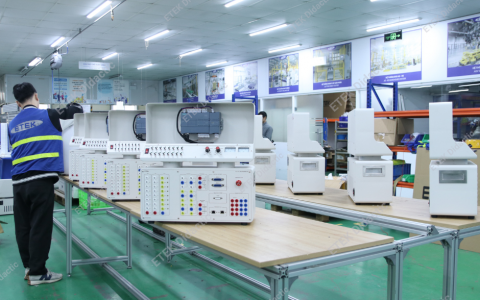
ETEK and the Technical Training Equipment Project for the University and College of Technical Technology Quy Nhon
_cr_480x300.png)
The project was implemented to create a training environment that closely simulates the actual procedures and conditions of an automotive assembly line.
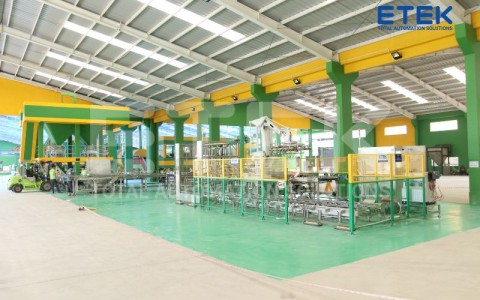
ETEK has successfully built a fully automatic bagging line, with a total output of up to 1200 bags/hour. The automated system includes a range of advanced equipment and technologies from automated conveying systems to bag printers, automated information checking and weight checking systems, along with detection and elimination capabilities Remove error envelopes.
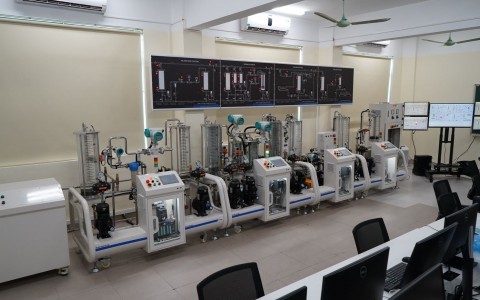
ETEK has successfully researched, designed, and constructed a Distributed Control System (DCS) training laboratory for the Electrical Engineering Department of the Hanoi University of Industry.
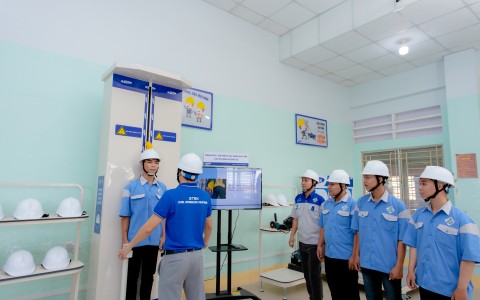
Successful research, design, and construction of rooms: Basic technical room; Basic electrical room; Equipped electrical practice room; Electrical machine practice room; Electrical installation practice room; Automation practice room serving practical training for students and lecturers.
_cr_480x300.jpg)
ETEK successfully constructed the thermal laboratory and industrial automation laboratory for Vinh Long University of Technical Education.
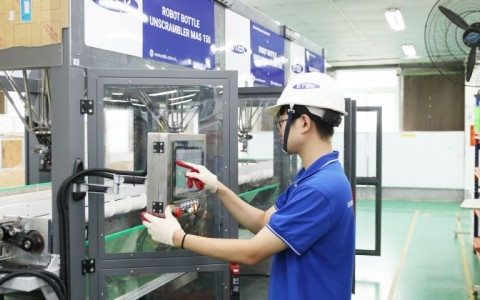
Our journey with Unilever factories in Vietnam, Indonesia, and the Philippines is a story of creating sustainable and professional automation solutions for fully automated consumer goods production lines, ensuring hygiene, safety, and aesthetics...
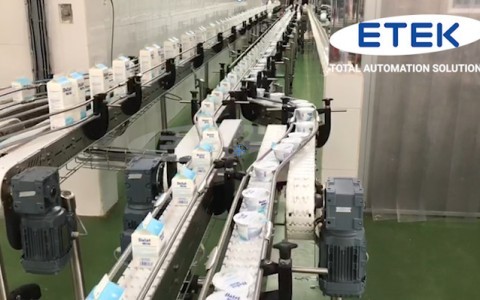
A manufacturer of children's boxed milk products in Da Lat aims to automate their product packaging lines to improve productivity, enhance efficiency, reduce costs, and eliminate the possibility of quality issues due to human error.
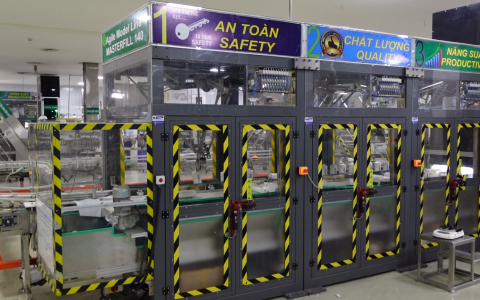
Driving digital transformation projects and focusing on building smart factories and intelligent supply chain management is the strategy of Unilever Vietnam.
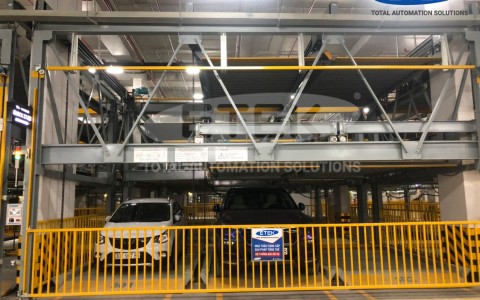
ETEK has completed the production and installation of the semi-automatic parking system project with 1,000 mechanical parking positions at the Symphony complex after nearly 7 months of construction.