ETEK Parking has implemented a 2-level smart puzzle parking system at the Phu Dong Sky Garden project, effectively solving the challenge of limited parking space.
PROVIDING MACHINERY AND AUTOMATION SYSTEMS FOR A JAPANESE COMPANY
Through nearly 15 years of cooperation and continuous learning from our Customers, ETEK has matured significantly in technical capability and has also achieved comprehensive improvement in processes, management mindset, and working culture. From the early, challenging projects to now, ETEK is honored to be a supplier of numerous machines and production lines, providing various specialized automation equipment for key stages in the industrial manufacturing process.
Cooperation Background
The year 2013 marked the beginning of the partnership between ETEK and our Customer – one of the world’s leading technology corporations from Japan, with decades of development and global presence. Our Customer is globally renowned in the field of imaging and optical equipment, with stringent operating procedures and high technical standards.
Being selected as a supplier of automation equipment for this Customer was not only an honor but also a major challenge for ETEK – a Vietnamese company still in the early stages of proving its capabilities in industrial automation.
Being selected as a supplier of automation equipment for this Customer was not only an honor but also a major challenge for ETEK – a Vietnamese company still in the early stages of proving its capabilities in industrial automation.
Product Portfolio
Through nearly 15 years of cooperation and continuous learning from our Customers, ETEK has matured significantly in technical capability and has also achieved comprehensive improvement in processes, management mindset, and working culture. From the early, challenging projects to now, ETEK is honored to be a supplier of numerous machines and production lines, providing various specialized automation equipment for key stages in the industrial manufacturing process.
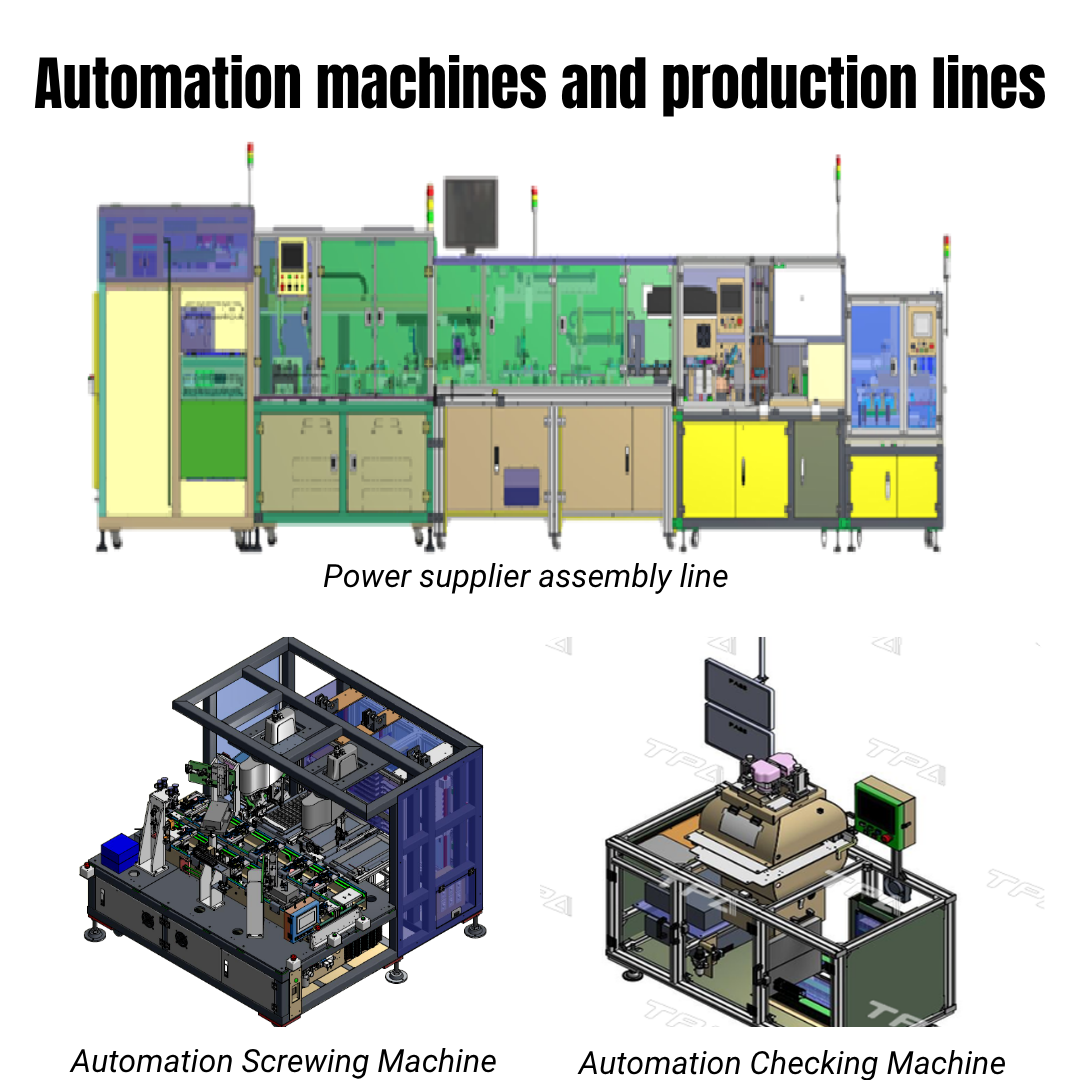
Before any system is officially handed over and put into operation at the Customer’s factory, it must go through a multi-layered inspection and evaluation process, jointly conducted by ETEK’s engineering team and the Customer’s technical representatives, following a rigorous procedure:
- Solution Consultation: From the very beginning, ETEK acts as a deep technical consulting partner. Our engineers research the structure of the products being manufactured, analyze detailed technical requirements of each production stage. Through direct meetings and discussions, both sides clarify needs, expectations, and technical constraints, thereby developing the most optimal automation solution—balancing technical features, production efficiency, and investment cost. This is a crucial foundation to ensure the equipment fits seamlessly into the Customer’s actual manufacturing environment.
- Detailed Design: Once the overall solution is agreed upon, ETEK proceeds with detailed design using modern design software. The drawings not only show the precise mechanical structure down to the millimeter, but also integrate critical elements such as: sensor placement, cable and air tube routing, maintenance access, and future scalability. All aspects are considered to ensure the equipment is easy to install – easy to operate – easy to maintain, while achieving optimal performance in actual operation.
- Machining and Assembly, with Step-by-Step Internal Inspections: After the design phase, the equipment is fabricated and assembled directly at ETEK’s manufacturing facility. The entire assembly process follows a standardized internal procedure, where each step has designated personnel, control forms, and tracking logs. After every assembly step (mechanical, electrical, pneumatic), internal inspections are carried out. This strict supervision minimizes errors and ensures consistent quality before proceeding to system testing.
- System Testing and Calibration: Before delivery, the system undergoes multiple evaluations and trial runs. During this phase, ETEK’s technical team works closely with the Customer’s Vietnamese technical staff.
- Final Evaluation Before Operation: Before being put into official use, the system undergoes real-world evaluation at the Customer’s factory. During this time, ETEK personnel work onsite, directly conducting trials and fine-tuning the system.
Customer Challenges and ETEK’s Growth Journey
As a leading Japanese technology corporation, the Customer is known for its business philosophy rooted in meticulousness, precision, and continuous improvement. This meticulousness is not only reflected in their products but is deeply embedded in their working culture.
The Customer’s products have highly specialized technical characteristics: complex component shapes, small sizes, and ultra-precise details that require accuracy down to a fraction of a millimeter. Each component—whether in printers, cameras, or optical devices—is optimized for performance but presents significant challenges for automated handling, inspection, and assembly.
Therefore, the equipment supplied to the Customer must not only meet high precision standards but also be designed to flexibly handle the unique shapes of the components. From part feeding, positioning, pick-place-tighten-weld operations to visual and electronic inspections, all processes must ensure stability without causing deformation or damage.
Beyond precision, optimizing layout and cycle time is also a critical requirement. The Customer’s production lines are tightly planned with limited space, so equipment must have a compact design, efficient layout, while still ensuring logical workflows, easy maintenance, and smooth operation.
In terms of cycle time, high processing speed is required without sacrificing stability. Thus, ETEK’s systems must be carefully calculated for the processing time of each stage, synchronized across modules, reduce idle time, and ensure output aligns with the production line rhythm.
This presented a significant challenge for ETEK – a Vietnamese company in the process of building a comprehensive ecosystem for designing and manufacturing automation systems.
Meeting the stringent requirements of a global corporation like our Customer required ETEK not only to master technical skills but also to continuously enhance its overall capacity – from design thinking, quality control processes, to project management and the ability to communicate technical matters with international clients.
Throughout the partnership, ETEK learned by doing, continuously improving. Each project provided our engineers with the opportunity to access international standards, gain deeper understanding of mechanical precision, optimize layouts for real-world applications, and most importantly, improve cycle time while maintaining equipment durability and stability.
Step by step, ETEK has built and developed a comprehensive ecosystem in the field of industrial automation.
The Customer’s products have highly specialized technical characteristics: complex component shapes, small sizes, and ultra-precise details that require accuracy down to a fraction of a millimeter. Each component—whether in printers, cameras, or optical devices—is optimized for performance but presents significant challenges for automated handling, inspection, and assembly.
Therefore, the equipment supplied to the Customer must not only meet high precision standards but also be designed to flexibly handle the unique shapes of the components. From part feeding, positioning, pick-place-tighten-weld operations to visual and electronic inspections, all processes must ensure stability without causing deformation or damage.
Beyond precision, optimizing layout and cycle time is also a critical requirement. The Customer’s production lines are tightly planned with limited space, so equipment must have a compact design, efficient layout, while still ensuring logical workflows, easy maintenance, and smooth operation.
In terms of cycle time, high processing speed is required without sacrificing stability. Thus, ETEK’s systems must be carefully calculated for the processing time of each stage, synchronized across modules, reduce idle time, and ensure output aligns with the production line rhythm.
This presented a significant challenge for ETEK – a Vietnamese company in the process of building a comprehensive ecosystem for designing and manufacturing automation systems.
Meeting the stringent requirements of a global corporation like our Customer required ETEK not only to master technical skills but also to continuously enhance its overall capacity – from design thinking, quality control processes, to project management and the ability to communicate technical matters with international clients.
Throughout the partnership, ETEK learned by doing, continuously improving. Each project provided our engineers with the opportunity to access international standards, gain deeper understanding of mechanical precision, optimize layouts for real-world applications, and most importantly, improve cycle time while maintaining equipment durability and stability.
Step by step, ETEK has built and developed a comprehensive ecosystem in the field of industrial automation.
Results and Long-term Relationship
From the early days filled with challenges, ETEK has now become a trusted and long-standing supplier. Both sides have maintained a sustainable partnership built on trust, collaboration, and continuous improvement.
ETEK’s continued selection for subsequent projects is the clearest testament to the quality of our products, our humble and learning attitude, and our team’s ability to adapt flexibly.
ETEK’s continued selection for subsequent projects is the clearest testament to the quality of our products, our humble and learning attitude, and our team’s ability to adapt flexibly.
Lesson learned
"The most demanding customer is the best teacher." ETEK believes that it is precisely through our Customer’s high expectations that we have grown to become more professional, more capable, and more prepared to conquer larger, more demanding markets in the future.
Others Projects
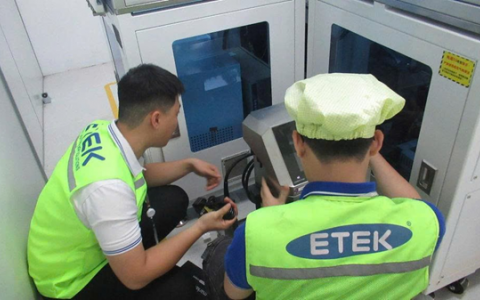
ETEK has successfully implemented a project to supply and install 5 Markem-Imaje 9750+ industrial inkjet printers for an electronic components factory. The project's goal is to replace old printing equipment and meet the increasing requirements for resolution and accuracy in printing micro QR codes on electronic products.

ETEK implemented the Pick to Light system for 15 Kitting areas and 7 Sequencing areas with a total of 3,575 components, reducing picking time, reducing errors and increasing productivity. The project included mechanical and electrical installation, integration with the manufacturing management system (MES) and operator training. The result: increased operational efficiency, synchronized data management, stable operation, meeting the high requirements of the automotive industry.
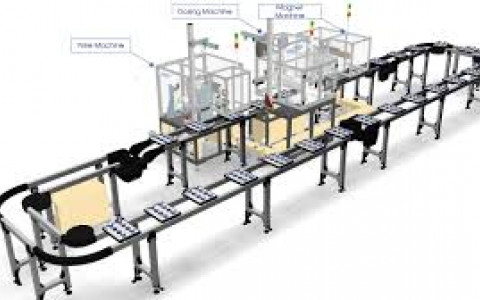
Client: A Japanese enterprise specializing in the production of auxiliary equipment for automobiles and motorcycles
Quantity: 01 assembly line
Project Name: Supply of Speaker Assembly Line
Quantity: 01 assembly line
Project Name: Supply of Speaker Assembly Line
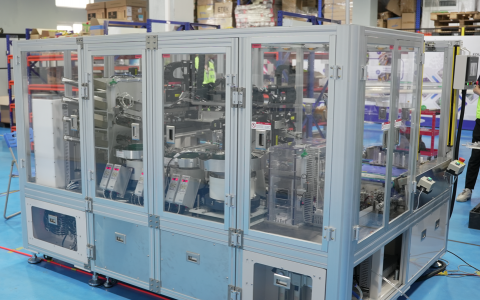
With the orientation of "long-term development with customers, built on technical expertise and sustainable responsibility," we are proud to continue our collaboration with a leading Japanese electronics partner on the Paper Roll Assembly Machine project – a challenging endeavor that stands as a testament to the trust and strong bond between our two companies
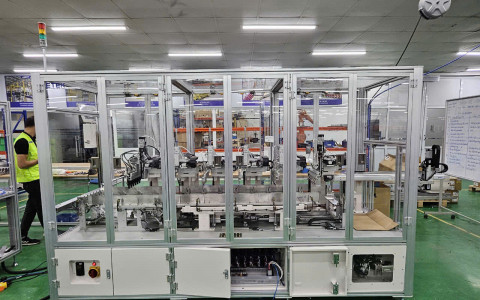
Client: A sports eyewear manufacturing company in China
Quantity: 01 machine
Machine Name: Anti-Fog Coating Machine for Swimming Goggles
Quantity: 01 machine
Machine Name: Anti-Fog Coating Machine for Swimming Goggles
_cr_480x300.png)
ETEK implemented an AGV (Automated Guided Vehicle) system for an automotive manufacturing and assembly plant, aiming to fully automate the transportation of materials, pallets, and trolleys throughout the production line.
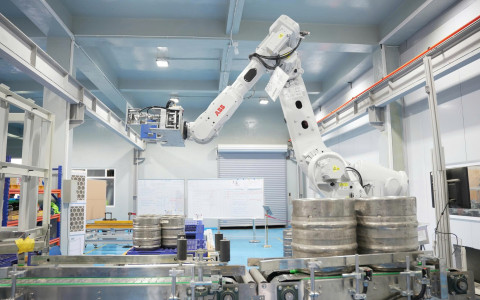
ETEK's automated palletizer system for 30L KEGs boosts production capacity to 400 KEGs/hour, minimizes manual labor, optimizes the process, and ensures stable, 24/7 operation with flexible settings for operational adjustments.
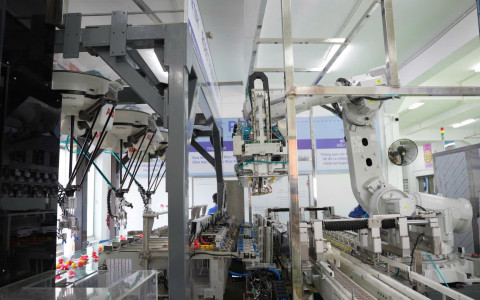
ETEK's automated pump cap tightening line boosts production speed, ensures consistent quality, and reduces operational costs while enhancing real-time defect detection and product removal during the production process.
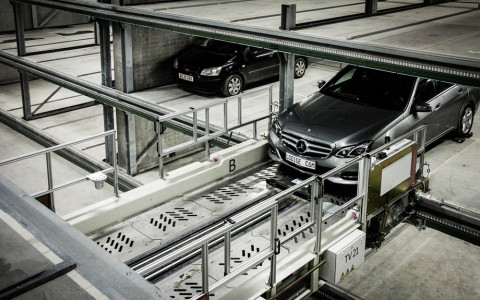
The automatic parking system maximizes the use of space across 3 underground levels, increasing parking capacity compared to traditional lots.
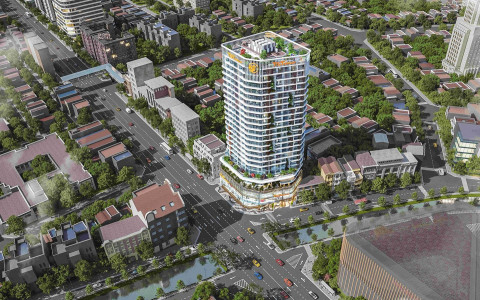
A semi-automatic parking system was deployed throughout all four basement levels, featuring a 2-level puzzle parking solution in each designated basement zone
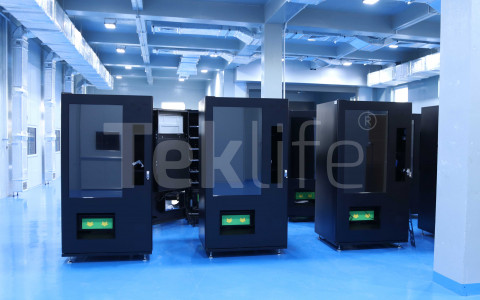
This model of automated product sampling serves not only as an innovative distribution channel, but also as a promising source of revenue for individual investors and product distributors.
_cr_480x300.png)
Case Study: ETEK Implements an Automated Production Line Training Solution at Thai Nguyen University of Technology
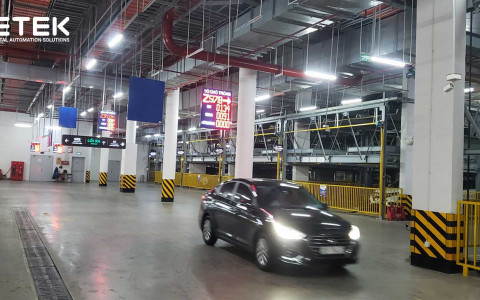
The semi-automatic 3-level puzzle parking system combined with a 2-level motorbike lift is an optimal parking model in terms of space utilization, operational efficiency, and cost-effectiveness.
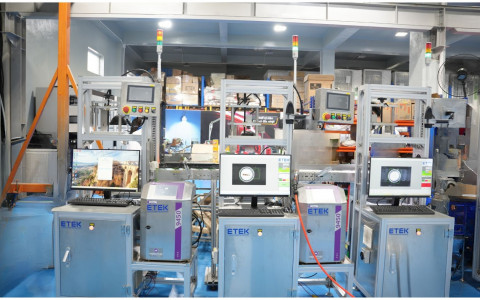
Our client is one of the leading corporations in the food and beverage industry, operating a high-capacity potato snack production line. To ensure product quality and meet the growing market demand, the client set strict requirements for the quality inspection system. ETEK successfully developed and implemented an automated solution for date printing and product quality inspection for the snack production line.
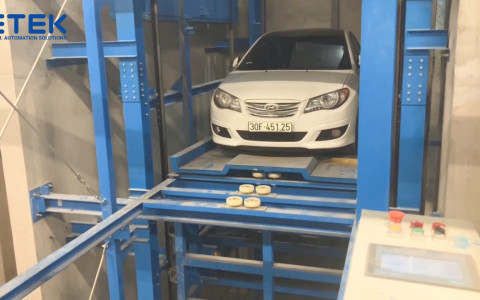
ETEK Parking has successfully implemented an automated parking system using Robocar technology in Quang Ninh – one of the most advanced technologies currently available in the field of automated parking.
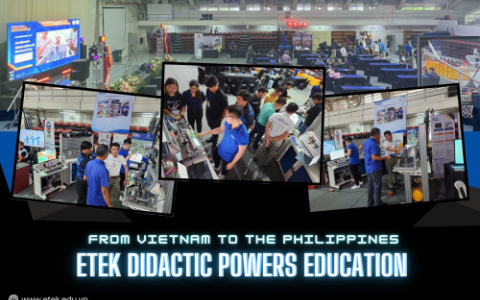
Case Study: From Vietnam to the Philippines – Delivering a Comprehensive Refrigeration Training Solution
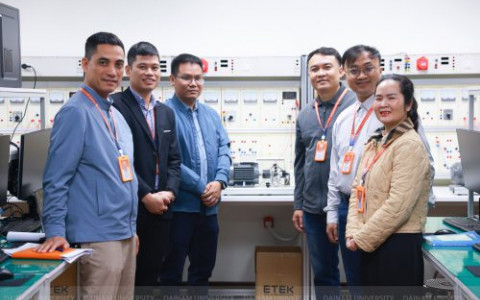
Case Study: ETEK Provides Technical Training Equipment for Dai Nam University
A Modern Training Solution with the Power Electronics Application Training Kit
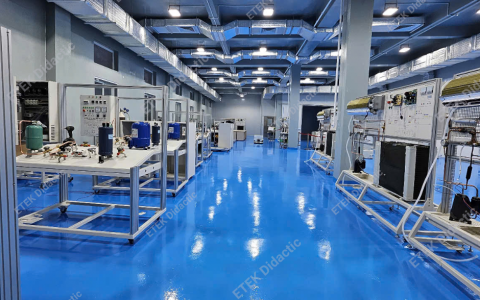
Case Study: ETEK Equips Vietnam Vocational College Korea Ha Noi City with Advanced Training Equipment
Client: Vietnam – Korea Vocational College
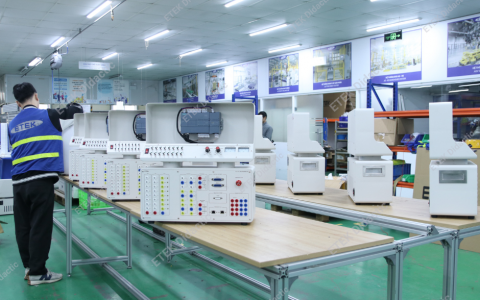
ETEK and the Technical Training Equipment Project for the University and College of Technical Technology Quy Nhon
_cr_480x300.png)
The project was implemented to create a training environment that closely simulates the actual procedures and conditions of an automotive assembly line.
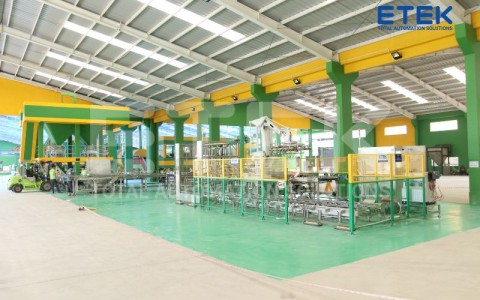
ETEK has successfully built a fully automatic bagging line, with a total output of up to 1200 bags/hour. The automated system includes a range of advanced equipment and technologies from automated conveying systems to bag printers, automated information checking and weight checking systems, along with detection and elimination capabilities Remove error envelopes.
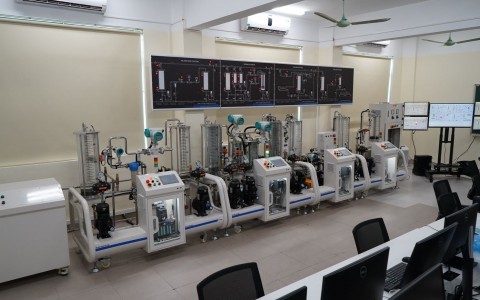
ETEK has successfully researched, designed, and constructed a Distributed Control System (DCS) training laboratory for the Electrical Engineering Department of the Hanoi University of Industry.
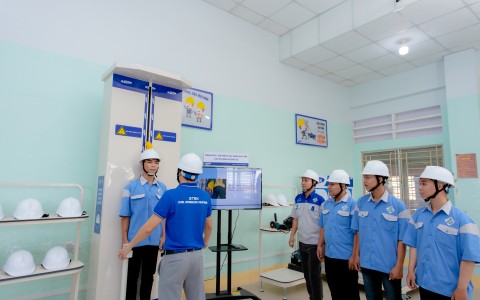
Successful research, design, and construction of rooms: Basic technical room; Basic electrical room; Equipped electrical practice room; Electrical machine practice room; Electrical installation practice room; Automation practice room serving practical training for students and lecturers.
_cr_480x300.jpg)
ETEK successfully constructed the thermal laboratory and industrial automation laboratory for Vinh Long University of Technical Education.
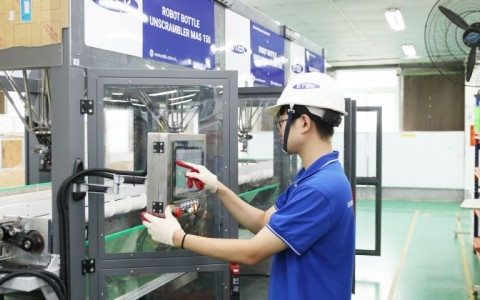
Our journey with Unilever factories in Vietnam, Indonesia, and the Philippines is a story of creating sustainable and professional automation solutions for fully automated consumer goods production lines, ensuring hygiene, safety, and aesthetics...
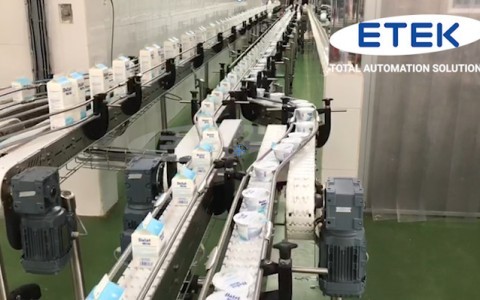
A manufacturer of children's boxed milk products in Da Lat aims to automate their product packaging lines to improve productivity, enhance efficiency, reduce costs, and eliminate the possibility of quality issues due to human error.
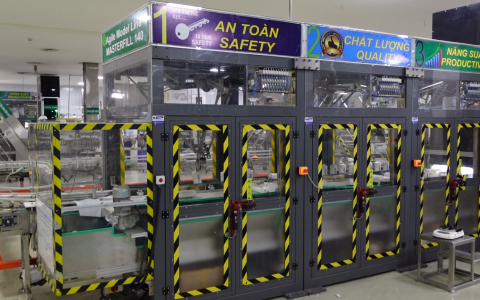
Driving digital transformation projects and focusing on building smart factories and intelligent supply chain management is the strategy of Unilever Vietnam.
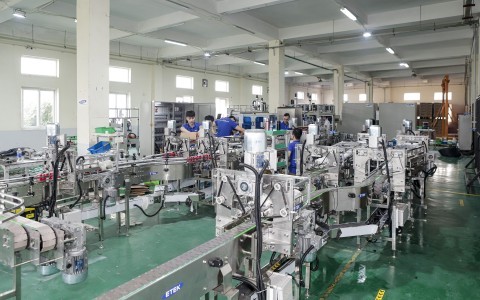
The soft drink manufacturing plant has built a packaging line to increase production output with twist conveyance technology for the first time introduced in Vietnam.
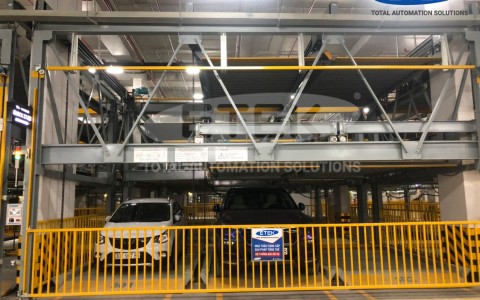
ETEK has completed the production and installation of the semi-automatic parking system project with 1,000 mechanical parking positions at the Symphony complex after nearly 7 months of construction.