ETEK Parking has implemented a 2-level smart puzzle parking system at the Phu Dong Sky Garden project, effectively solving the challenge of limited parking space.
Quantity: 01 machine
Machine Name: Anti-Fog Coating Machine for Swimming Goggles
Background and Challenges
This is ETEK’s first project with a Chinese customer, marking a significant milestone in our strategy to expand into new markets and diversify our customer base in the optical and sports equipment sector.
The customer is a high-end swimming goggles manufacturer with stringent requirements for anti-fog coating quality. Key technical challenges included:
- A wide variety of product models, including flat, curved, and holed lenses
- Required coating thickness: 2 µm < x < 5 µm
- The glue must not overflow, clog holes, or stick to the opposite surface
- Production cycle requirement: 800 units/hour
ETEK’s Design Solution
ETEK provided a custom-designed automatic coating machine, tailored precisely to the customer’s technical specifications.
Technical Specifications:
- Machine dimensions: 4100 x 1200 x 2000 (mm)
- Product model compatibility: Adaptable to three different product models
- Production capacity: 800 units/hour
The system is composed of three main modules:
- Motion mechanism: A high-precision lifting structure is used to transfer products and jigs, minimizing positional errors and ensuring long-term stability
- Coating and jig transfer mechanism: The coating process and jig transfer are separated to ensure stability and avoid interference
- Excess glue suction mechanism: 5 suction positions operate in stages to completely remove excess glue, preventing overflow or hole clogging
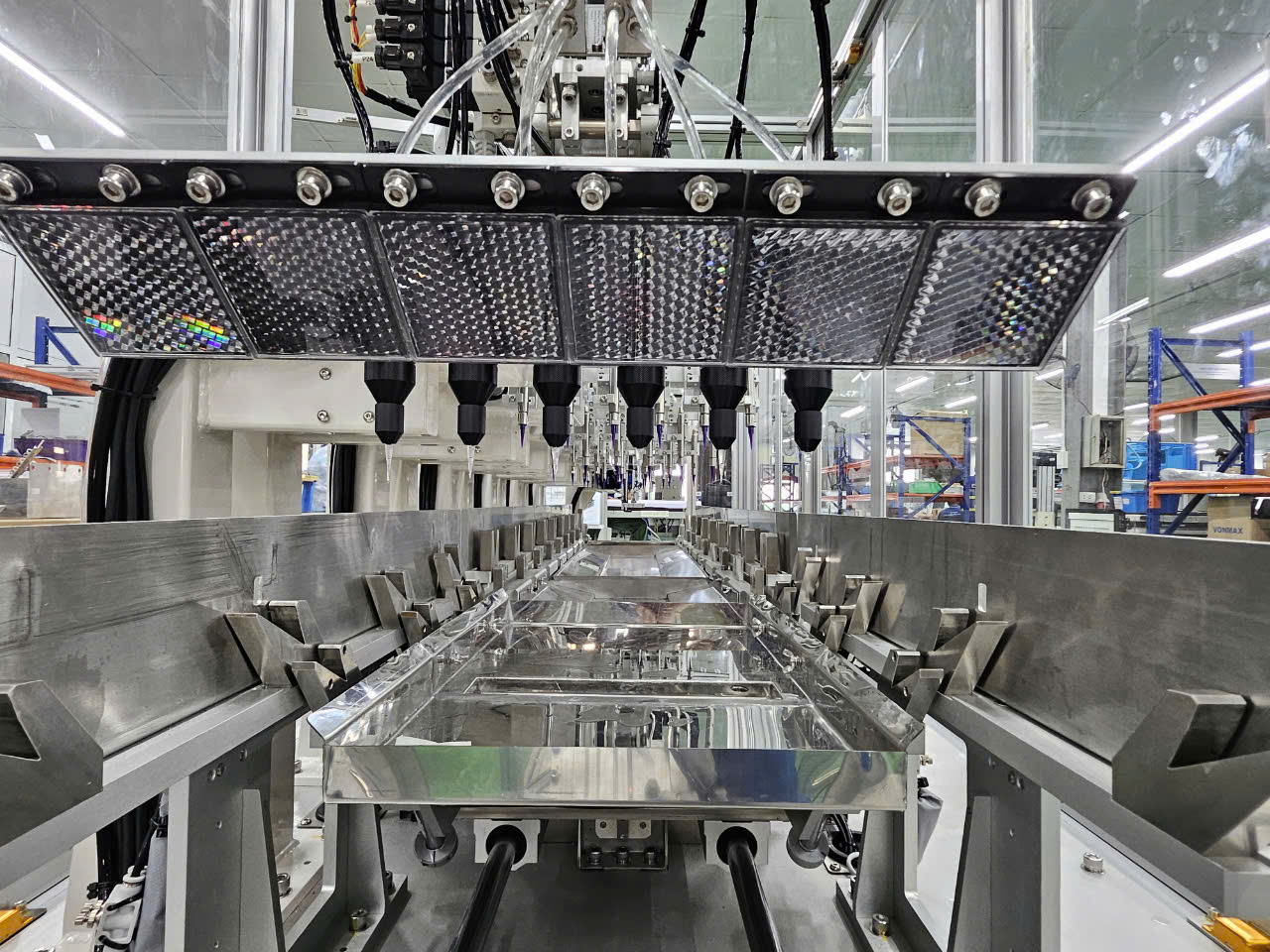
Project Implementation Process
Before final delivery and on-site operation, each system underwent a multi-layered inspection and evaluation process, conducted collaboratively by ETEK's engineers and the client’s technical representatives.
- Solution Consulting:
From the early stages, ETEK served as a technical consulting partner. Our engineers studied the client's product structure and analyzed technical requirements for each process step.
Through direct meetings, both parties clarified needs, expectations, and constraints, leading to the development of an optimized automation solution that balanced performance, efficiency, and investment cost.
This foundational step ensured the solution was well-aligned with actual production conditions at the factory.
- Detailed Design:
After the overall concept was approved, ETEK developed detailed designs using advanced CAD tools.
The design not only ensured mechanical precision down to the millimeter but also integrated elements like sensor placements, cable and air line routing, maintenance access, and future expansion potential.
Everything was considered to ensure the machine is easy to install, operate, and maintain while delivering optimal performance.
- Fabrication and Assembly with Internal Checks at Every Stage:
Once the design was finalized, the machine was fabricated and assembled at ETEK’s production facility.
The assembly followed a standardized internal process, with assigned responsibilities, control forms, and tracking logs at every step.
Each stage of assembly (mechanical, electrical, pneumatic) included internal quality checks.
This strict supervision minimized errors and ensured consistent quality before testing.
- System Testing and Calibration:
Prior to delivery, the system underwent multiple evaluations and trial runs. During this time, ETEK’s engineers worked closely with the customer’s technical team.
- Final Evaluation Before Operation:
Before being put into use, the system underwent final assessments at the client’s factory.
ETEK personnel were onsite to conduct test runs and fine-tuning.
Thanks to this meticulous preparation, ETEK machines consistently meet the toughest demands, operating reliably over the long term.
Results Achieved
The project fully met the customer’s stringent technical requirements, including: High coating quality, operational precision, fast production cycle, etc...
Notably:
- On-time delivery ensured the customer’s production schedule was maintained
- The machine operated smoothly with zero errors during both testing and actual production
- The customer highly appreciated ETEK’s professionalism and transparent project execution, despite it being our first collaboration
This trust and positive feedback motivate ETEK to continue demonstrating its capabilities and strengthening its reputation in the specialized automation industry.
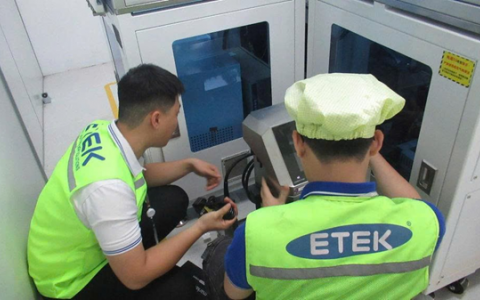

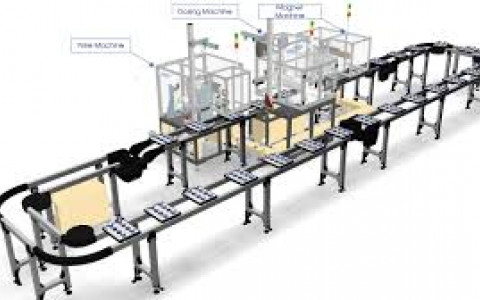
Quantity: 01 assembly line
Project Name: Supply of Speaker Assembly Line
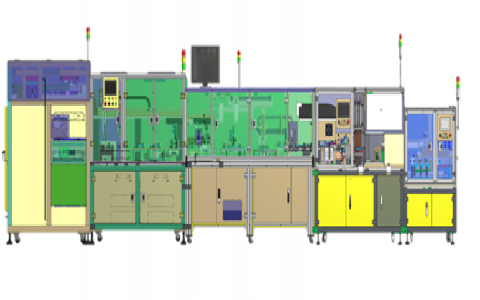
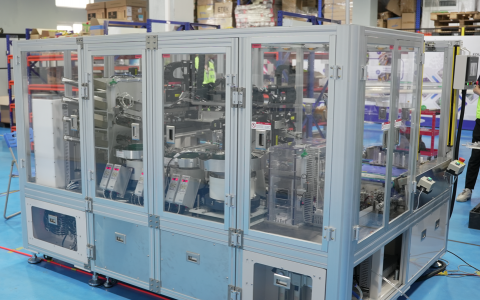
With the orientation of "long-term development with customers, built on technical expertise and sustainable responsibility," we are proud to continue our collaboration with a leading Japanese electronics partner on the Paper Roll Assembly Machine project – a challenging endeavor that stands as a testament to the trust and strong bond between our two companies
_cr_480x300.png)
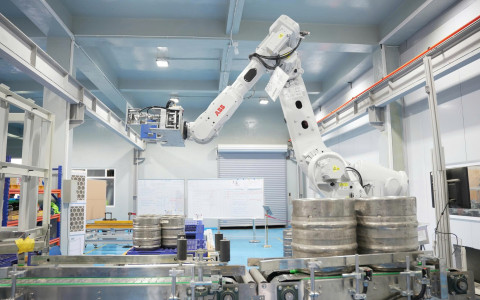
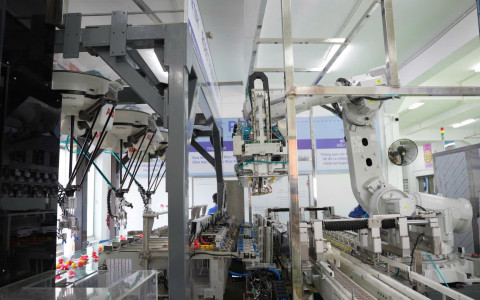
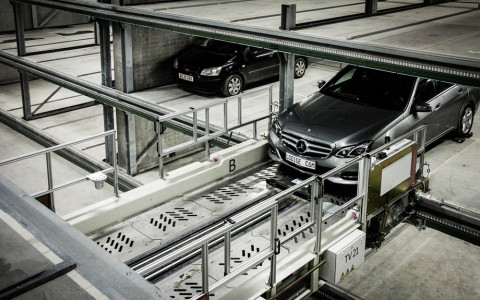
The automatic parking system maximizes the use of space across 3 underground levels, increasing parking capacity compared to traditional lots.
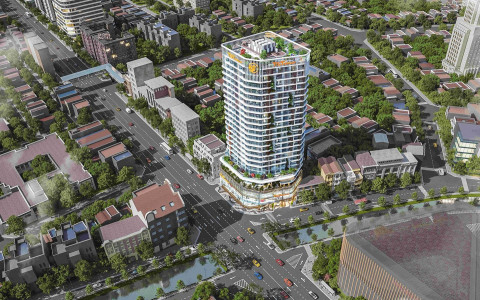
A semi-automatic parking system was deployed throughout all four basement levels, featuring a 2-level puzzle parking solution in each designated basement zone
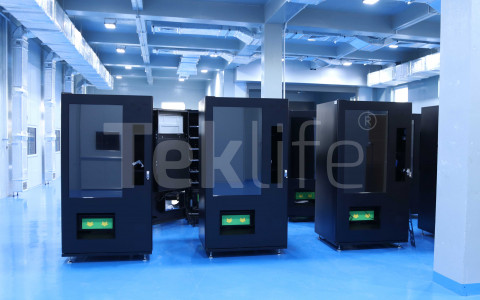
_cr_480x300.png)
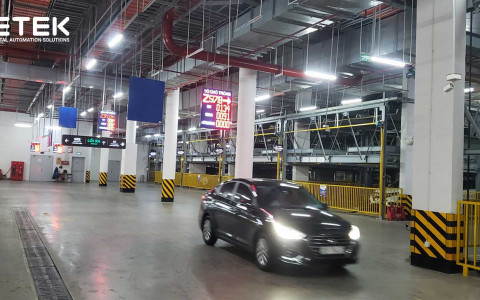
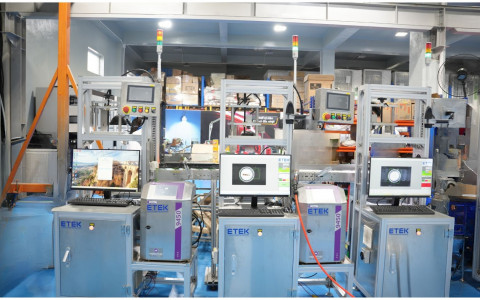
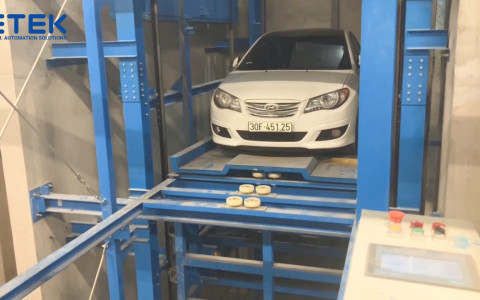
ETEK Parking has successfully implemented an automated parking system using Robocar technology in Quang Ninh – one of the most advanced technologies currently available in the field of automated parking.
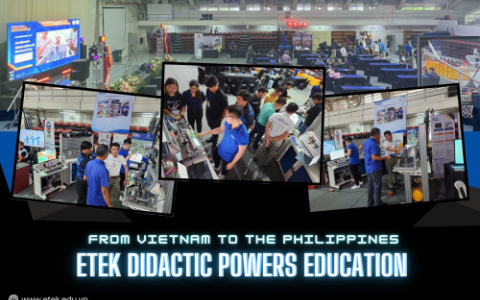
Case Study: From Vietnam to the Philippines – Delivering a Comprehensive Refrigeration Training Solution
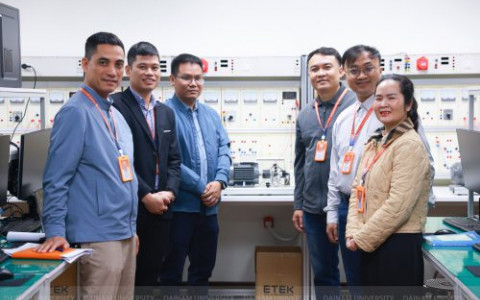
Case Study: ETEK Provides Technical Training Equipment for Dai Nam University
A Modern Training Solution with the Power Electronics Application Training Kit
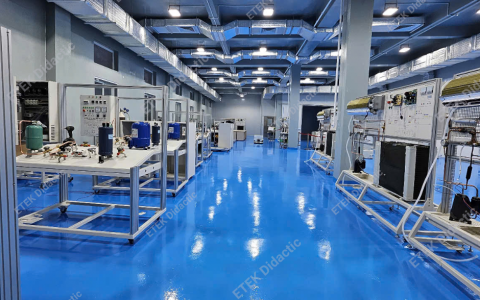
Case Study: ETEK Equips Vietnam Vocational College Korea Ha Noi City with Advanced Training Equipment
Client: Vietnam – Korea Vocational College
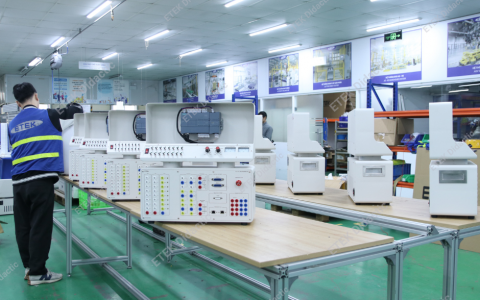
_cr_480x300.png)
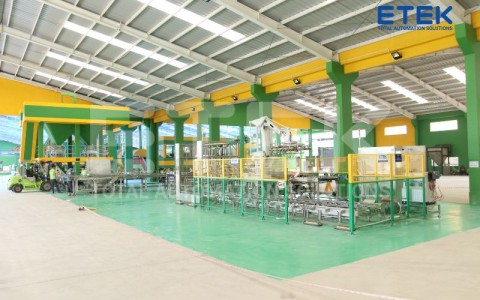
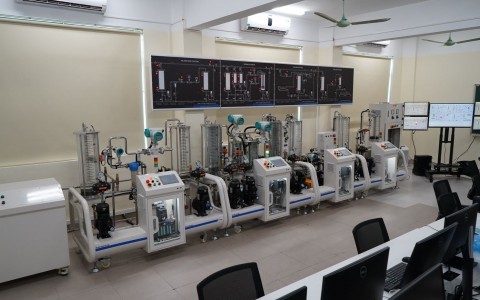
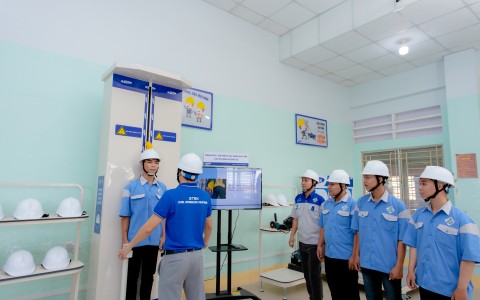
_cr_480x300.jpg)
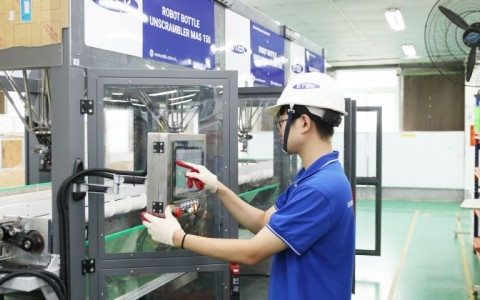
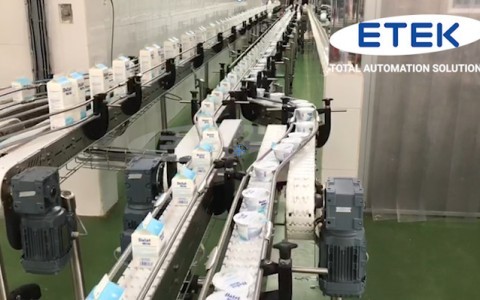
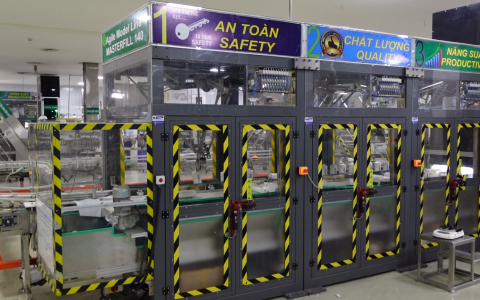
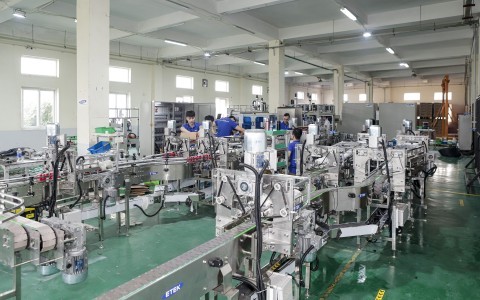
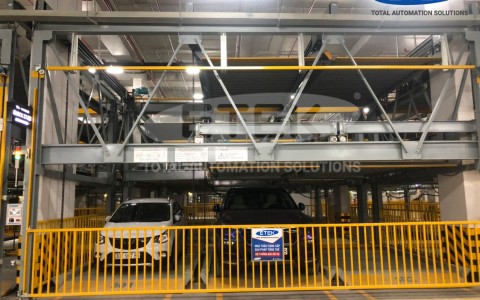