The client's problem
Production capacity
The manual operation of the factory's production lines resulted in low productivity, unable to meet the increasing demand for orders. Hiring more workers to increase productivity would also lead to higher costs and is not a sustainable solution in the modern technological era.
Product accuracy
Manual operation of barcode printing and product barcode verification also led to many errors.
Client requirements
Automation
Provide an automated production line connecting from the bagging machine to pallet stacking, including automatic bag weighing, product information printing, and error reporting.
Production output and time
The pressure to increase production output is becoming increasingly urgent for factories and businesses, requiring them to find innovative solutions to meet demand and gain market share in a competitive market.
Product quality
Products must be accurate in terms of both weight and information, thereby reducing costs due to errors compared to manual processes.
Safety
The production line must ensure 100% safety during operation.
Factory digitization
The company's desire for digitization reflects their eagerness to adapt to the modern market and maximize the potential of technology. And automating the production line is the first step in the digitization process.
ETEK's solution
After receiving the client's requirements, we implemented a comprehensive automation process to complete the project in a short period of just over 4 months. This process includes stages from consulting, requirement analysis, technical design, deployment planning, to installation and product handover to customer.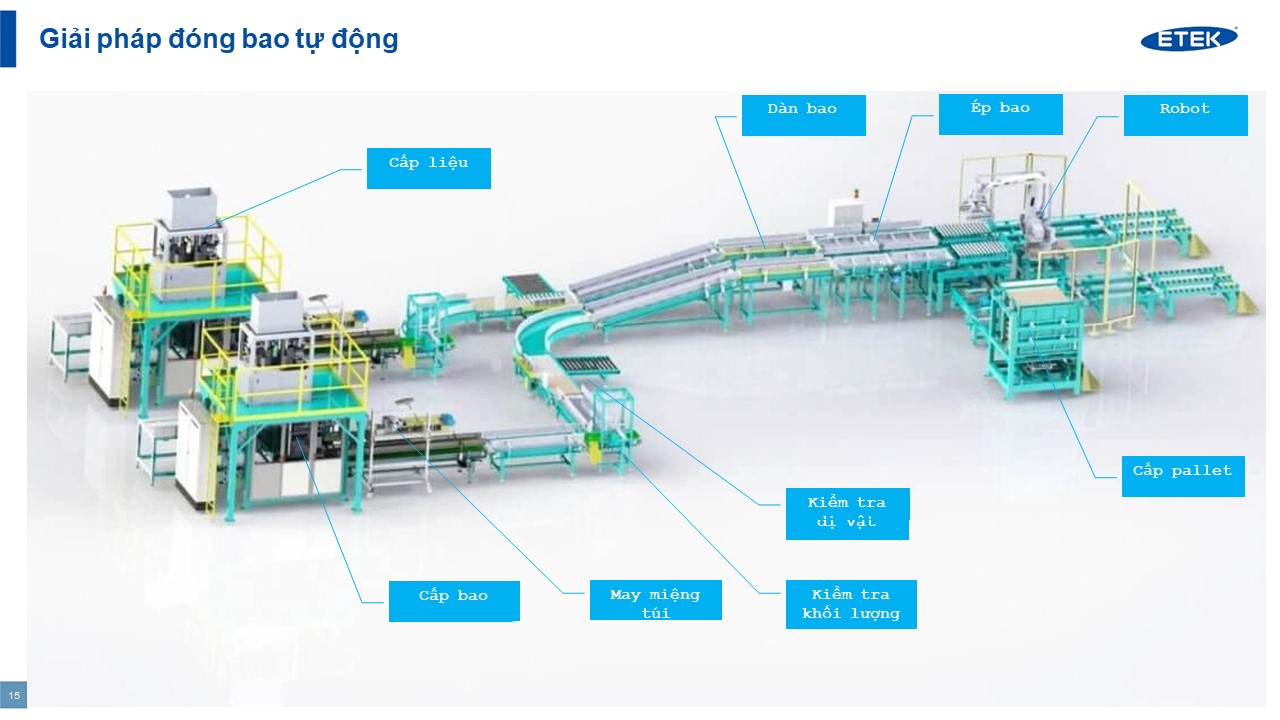
ETEK has successfully built a fully automated bagging line with a total production capacity of 1200 bags/hour. These lines are not only designed to meet the packaging needs of two different types of bags weighing 25kg and 50kg, but are also integrated with the latest technologies to optimize performance and flexibility.
Our automated system includes a range of advanced equipment and technologies from automated conveyors to bag printers, automated information and weight checking systems, along with the ability to detect and remove defective bags. This helps us ensure that the production process runs smoothly and efficiently, minimizing human intervention and increasing automation in the production process.
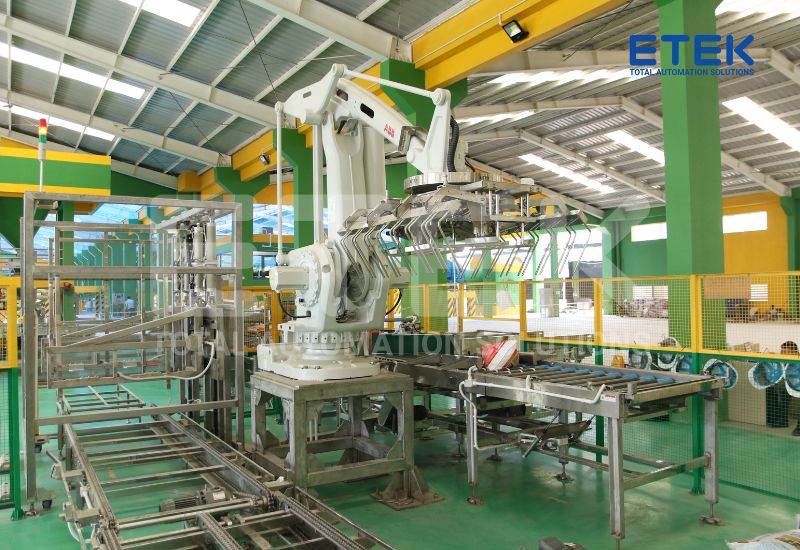
The system includes:
- PVC bag conveyor belt: Transports bags to the filling and sewing area
- Bag turning conveyor: Transfers bags from standing to lying position
- Bag spreading conveyor: Spreads the product evenly inside the bag
- Bag pressing conveyor: Flattens the bag surface before printing
- Bag weighing conveyor: Automatically weighs the weight of the bags on the conveyor belt, ensuring the correct weight of the product
- Production information printer: Automatically prints bag sequence numbers, prints unique QR codes for each bag, and issues warnings when the camera is not working.
- Conveyor for sorting out substandard products
- Robot pallet stacking conveyor
Results achieved
- Increased productivity by 150%
- Reduced costs by 20%
- Reduced product defects to <5%
- Factory digitization >50%
- Ensured labor safety