Providing DCS training lab solution for Hanoi University of Industry
ETEK has successfully researched, designed, and constructed a Distributed Control System (DCS) training laboratory for the Electrical Engineering Department of the Hanoi University of Industry.
The Electrical Engineering Department at Hanoi University of Industry offers quality training programs in electrical engineering and technology to meet the workforce demand in this field. With an experienced team of lecturers, the department provides in-depth training in various undergraduate and postgraduate majors.
Additionally, the university has other requirements to meet the needs of specialized training, providing practical experience for students. The practice room needs to be equipped with necessary equipment and ensure a safe environment with guidance for students on safety regulations during learning and practice. The practice room provides a variety of practical exercises and creates a dynamic learning environment, encouraging learners to exchange opinions and solve problems similar to real-world scenarios.
1. Ideation
The initial step involves identifying the skills to be trained, the department's needs, the school's requirements, and the necessary technologies and equipment for the laboratory. Ensuring that the skills and knowledge of related disciplines are adequately trained in the practice room.
2. Continuous review meetings
This is an important stage to gather opinions and feedback from relevant parties. Experts, management teams, and teachers present and unify ideas with each other and evaluate to reach a common solution.
3. Revisions
Based on feedback from the review meetings, proceed to revise the initial plan. This may include changes in room design, addition or removal of training elements, and adjustments to budget or schedule. Factors such as physical space, equipment, software, study materials, and training activities need to be considered.
4. Finalizing the solution
After completing the revisions, present the final solution for the DCS training laboratory. Specify details regarding room size and layout, proposed necessary equipment, selection of training software and study materials, as well as specific training activities and methods.
The DCS system was built in the practice room to meet various subject requirements. Practicing with DCS, students experience, learn, and directly interact with simulation devices as in food and beverage processing plants, oil and gas industry, water treatment systems, manufacturing industries. These are also popular sectors where Electrical Engineering students work after graduation.
Requirements from the Electrical Engineering Department, Hanoi University of Industry, for ETEK
For the department
Having a DCS practice room for students to practice after lectures, with visual tools for instructors to guide students after theoretical classes.For students
To learn and practice visually, to have access to new technologies, and to create high-quality human resources with advanced skills.For the supplying unit
Being a reputable unit with experience in providing equipment, experienced in developing laboratory solutions to ensure standards and meet requirements.Additionally, the university has other requirements to meet the needs of specialized training, providing practical experience for students. The practice room needs to be equipped with necessary equipment and ensure a safe environment with guidance for students on safety regulations during learning and practice. The practice room provides a variety of practical exercises and creates a dynamic learning environment, encouraging learners to exchange opinions and solve problems similar to real-world scenarios.
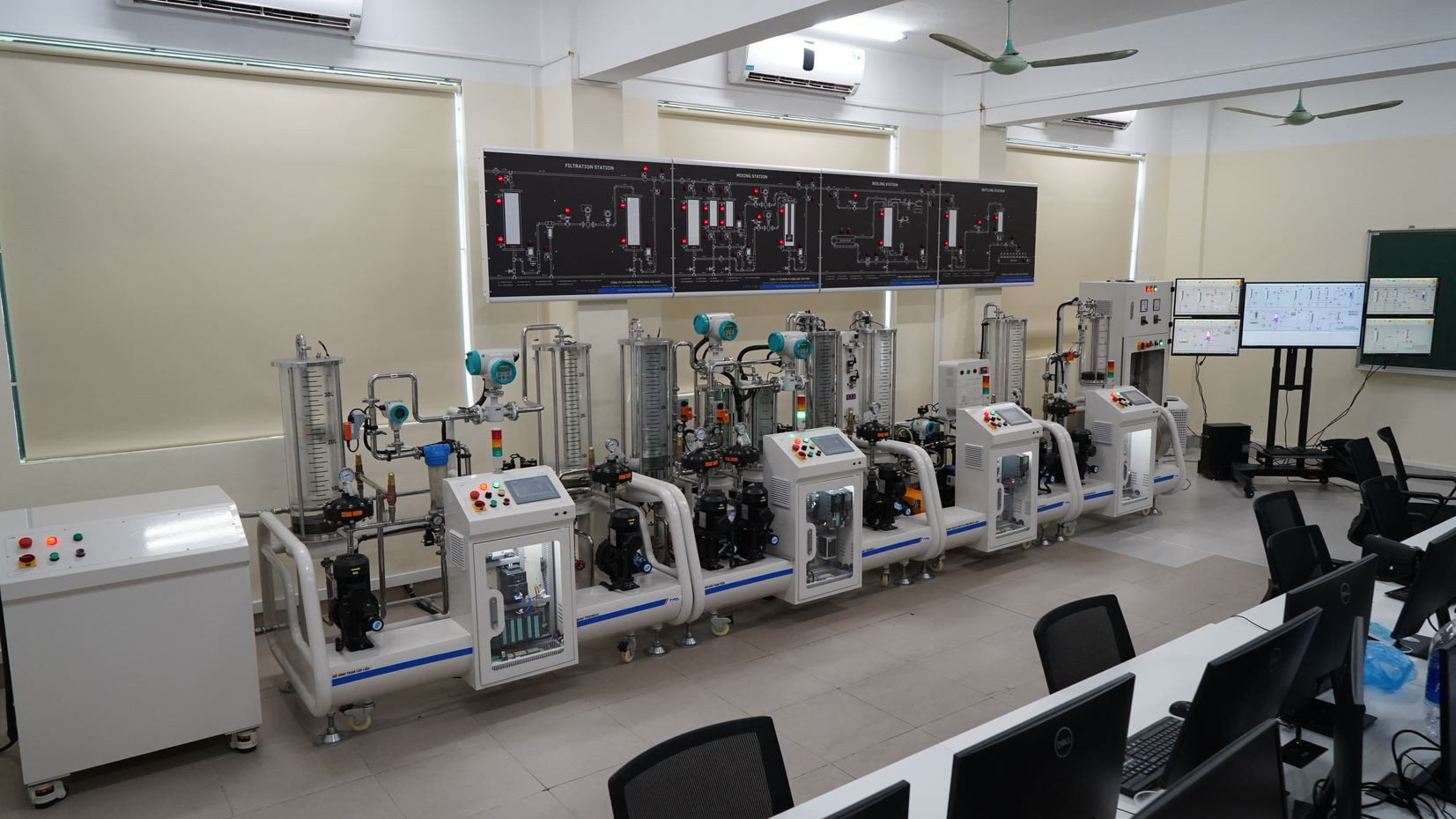
Upon receiving the request, ETEK promptly planned the solution implementation with standard steps such as ideation, review meetings, revisions, finalizing the solution, while continuously communicating with the customer about ideas, requirements, and ensuring ETEK's compliance with the school's and department's demands. ETEK's Solutions and Challenges in Building the DCS Training Laboratory
1. Ideation
The initial step involves identifying the skills to be trained, the department's needs, the school's requirements, and the necessary technologies and equipment for the laboratory. Ensuring that the skills and knowledge of related disciplines are adequately trained in the practice room.
2. Continuous review meetings
This is an important stage to gather opinions and feedback from relevant parties. Experts, management teams, and teachers present and unify ideas with each other and evaluate to reach a common solution.
3. Revisions
Based on feedback from the review meetings, proceed to revise the initial plan. This may include changes in room design, addition or removal of training elements, and adjustments to budget or schedule. Factors such as physical space, equipment, software, study materials, and training activities need to be considered.
4. Finalizing the solution
After completing the revisions, present the final solution for the DCS training laboratory. Specify details regarding room size and layout, proposed necessary equipment, selection of training software and study materials, as well as specific training activities and methods.

Achievements
ETEK designed and built the DCS training laboratory
ETEK proposed a Distributed Control System (DCS) solution. This system controls a production line, process, or dynamic system. However, the control is not centralized in a specific area but distributed with sub-systems operated by one or more separate controllers.The DCS system was built in the practice room to meet various subject requirements. Practicing with DCS, students experience, learn, and directly interact with simulation devices as in food and beverage processing plants, oil and gas industry, water treatment systems, manufacturing industries. These are also popular sectors where Electrical Engineering students work after graduation.
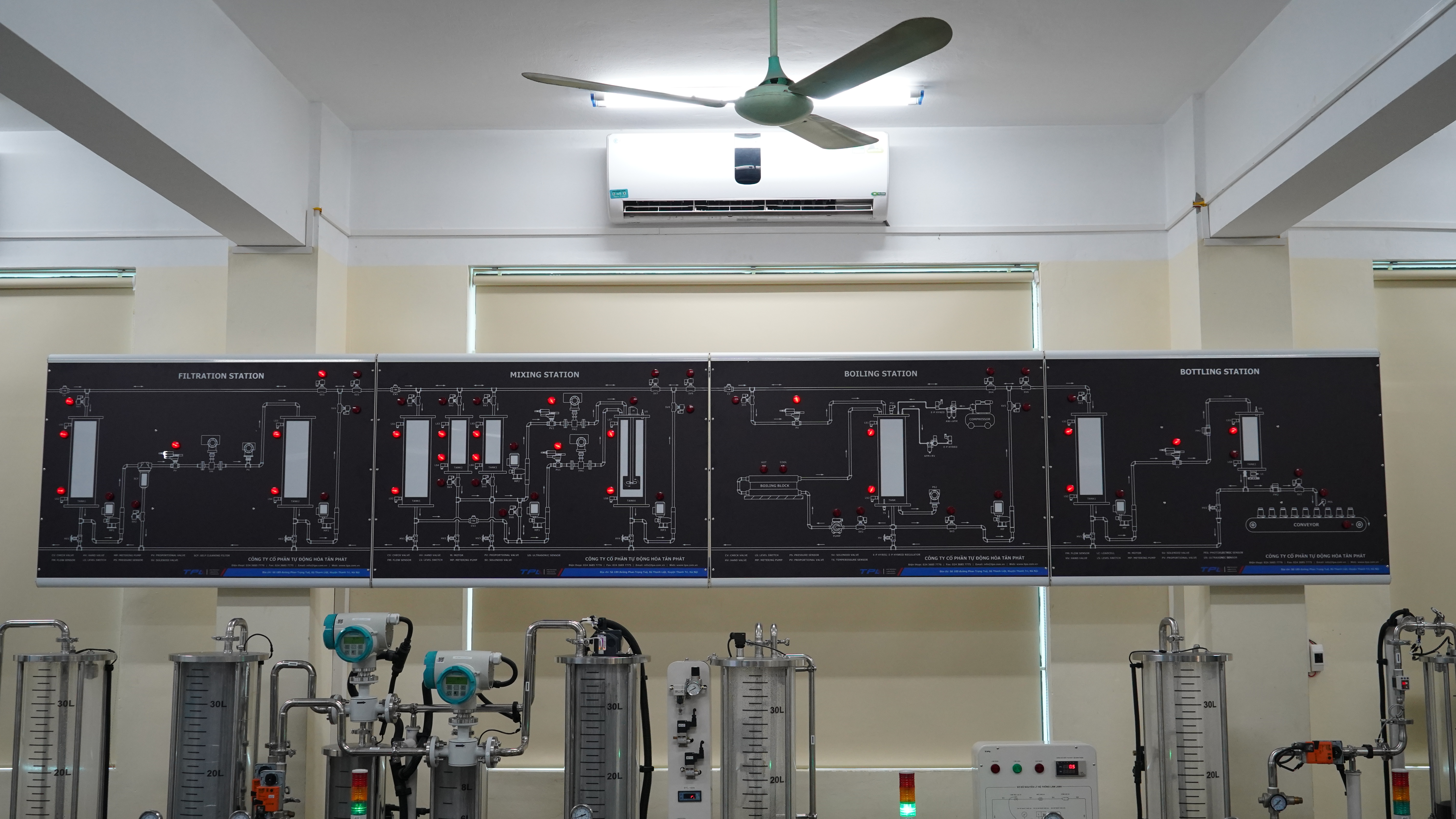
Meeting the training needs of the department and students
The solutions that ETEK built and deployed in the practice room fully meet the criteria and cover the content of many subjects. Basic training content on process control systems includes:- Survey, understanding of system working principles: Principles of sensors; Actuators, controllers
- Setting up On-Off control problems: Pressure control, flow control, level control, flow control. Pressure, temperature. Level, mass, flow
- Setting up PID control problems level control through the pressure and height relationship of the water column
- Interactive control: Temperature - water level.
- Multivariable control: Ratio - level
- Practical route control
- Coordination of batching problems, using mass sensors
- Testing, maintenance, and system maintenance
- Device configuration and sensor setup
- Setting up PID control problems pressure control, flow control, level control, mixing ratio control, heat exchanger temperature control, mass control
- Interactive control: Temperature - water level
- Batch control practice
- Operating and monitoring the system