Total solution for electric vehicle engine assembly line
Our client is a leading Vietnamese electric car manufacturer with a production capacity of 25,000 vehicles per year, aiming to reach 100,000 vehicles annually by 2025.
Factory Challenges
Assembly Standards
SAFETY - ENVIRONMENTAL FRIENDLINESS - COST EFFICIENCY are the top three criteria that users consider when deciding to purchase an electric car. Ensuring the safety and quality of the product poses the greatest challenge for both the customer and ETEK in developing a comprehensive solution for the electric engine assembly line.Overall Solution
Embracing the trend of environmental-friendly manufacturing by shifting towards electric vehicles is a significant and risky transformation for our client. Adapting to entirely new technologies poses difficulties in altering production processes. The total solution for the electric engine assembly line needs to be designed swiftly to keep up with the client's business transition.Engine Assembly Productivity
The overall production capacity target is set at 25,000 vehicles per year, increasing to 100,000 vehicles by 2025 to secure an early market presence and enhance brand competitiveness. The engine assembly workshop is crucial in determining the success of these production goals.New Technologies
During the construction of the electric engine assembly line, electric vehicles were still a new concept, with only major companies like Tesla and BYD developing such technologies. Our client was the first in Vietnam and a pioneer in Southeast Asia. The implementation of new technologies in the engine assembly line was challenging due to their novelty and limited accessibility.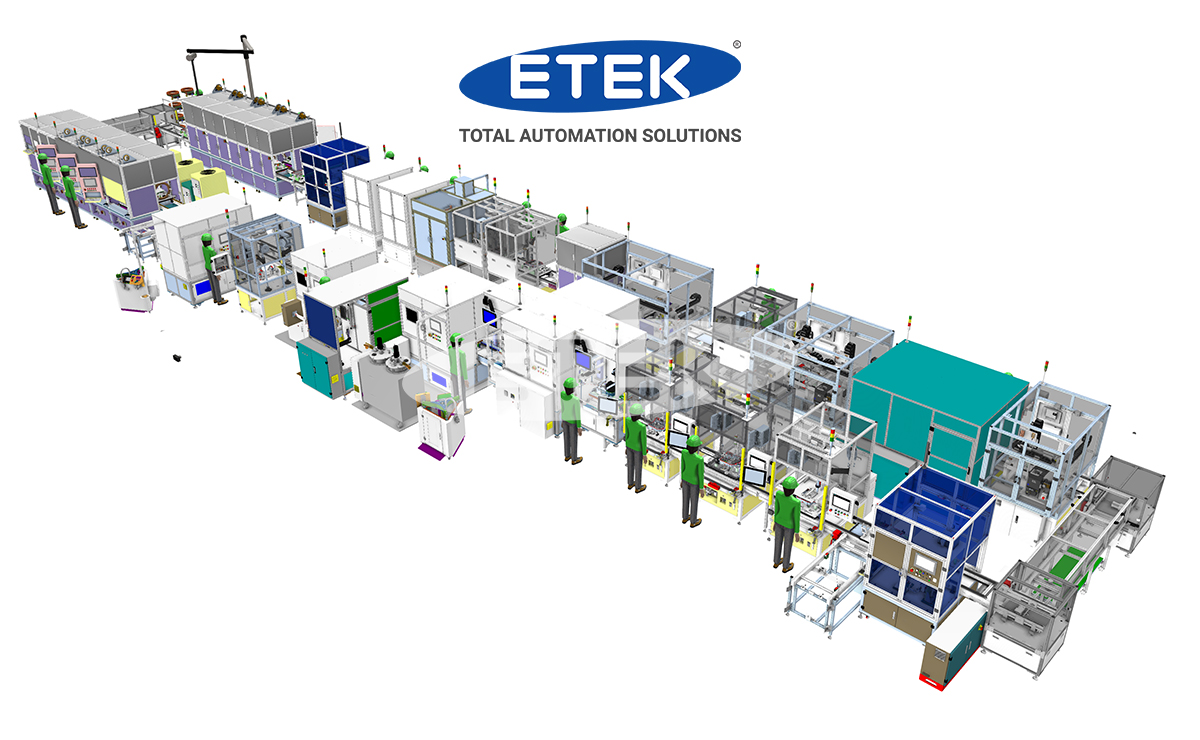
Project Competition
Competitors
The engine assembly workshop is a large-scale project with fierce competition from major players in automation in Vietnam. Additionally, competitors from China, India, South Korea, and others are formidable opponents. Some competitors have prior experience in supplying and installing engine assembly lines for the client's manufacturing system.Technology Solutions
Optimizing engine assembly technology and collaborating on problem-solving with the factory are essential requirements for all participating contractors. The application of modern technologies worldwide is necessary for the assembly line.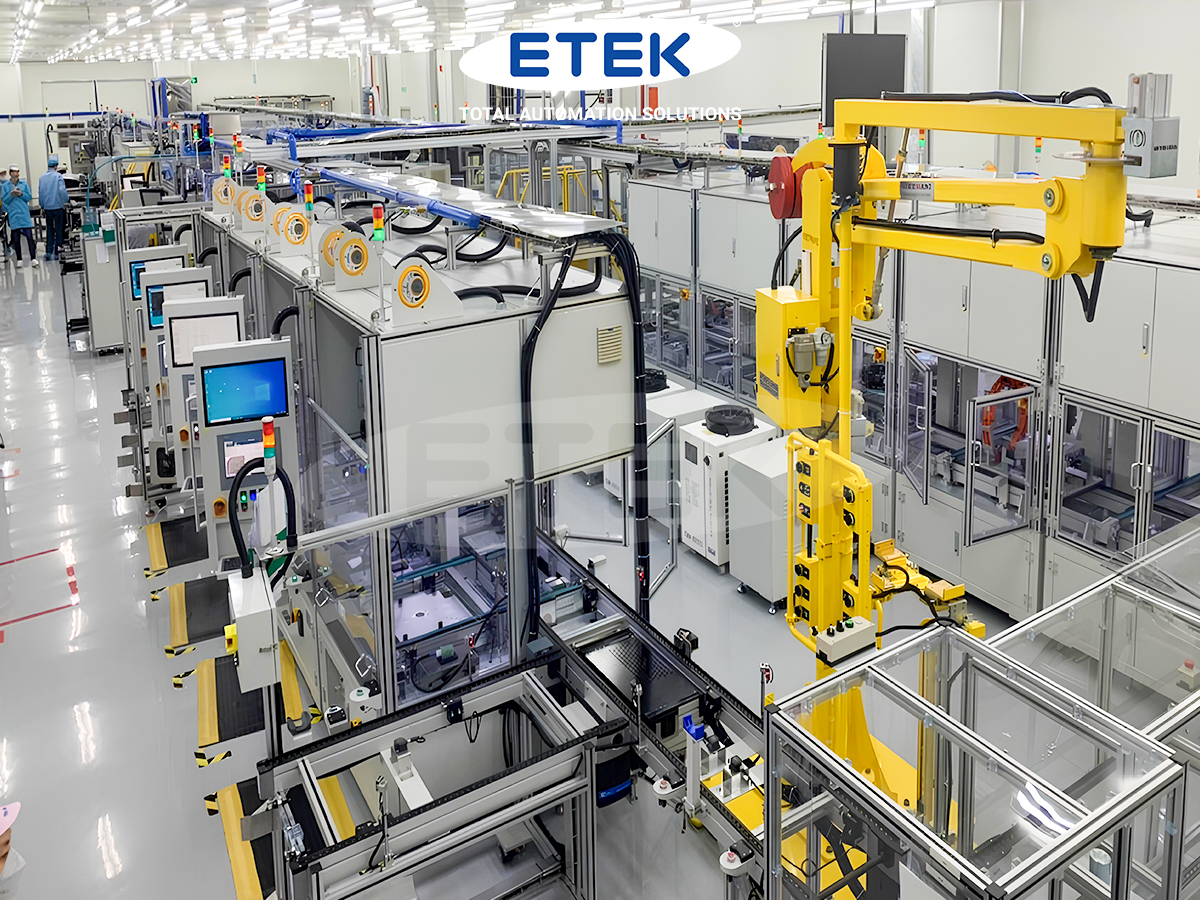
ETEK's Solutions
General Contractor
With 17 years of experience in leading automation in Vietnam, ETEK proudly offers pioneering comprehensive solutions across various sectors. Leveraging this advantage, we have developed an engine assembly solution based on three main criteria: Safety, Technology, and Automation.Technology Transfer
We transfer technology from leading experts in our partner's field, providing three core technologies for the engine assembly line:- EOL Test Technology: Testing technique for gas leaks, errors, and defect detection in the production line.
- Aging Technology: Product aging - a core technology enabling electric vehicles to withstand harsh environmental conditions.
- Cleanroom Technology: Class 9 standard for battery and electric vehicle engine production according to EU standards.
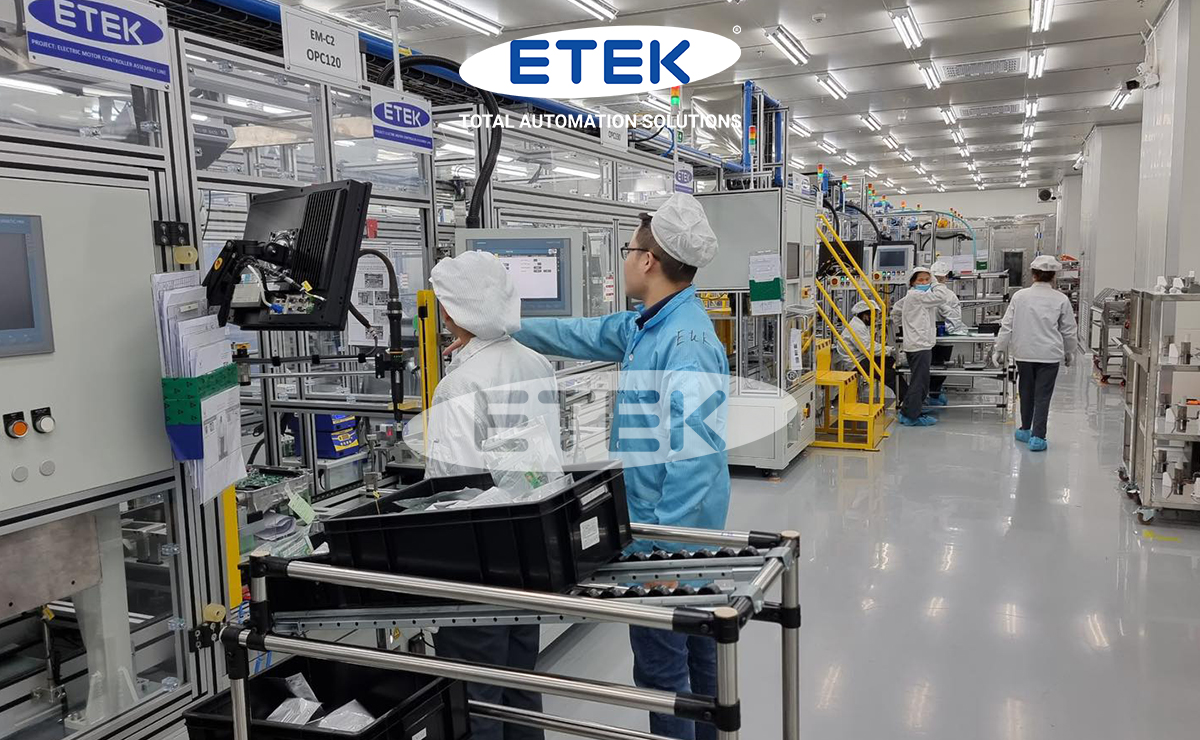
Challenges
Project Scale
This is the largest comprehensive solution for engine assembly to date, with a Vietnamese contractor undertaking 100% of the project. The engine assembly project includes over 100 stages with 40 different assembly station designs of high complexity. The factory's capacity requires 40 products per hour compared to the previous 25 products per hour.Deployment Time
The project is deployed simultaneously with multiple manufacturing and assembly lines, demanding a rapid schedule to seamlessly integrate the overall process. International cargo transportation during the project in the early 2020s posed additional challenges. Setting a deadline with the customer and the need for early production further increased pressure on the schedule.Technology - Design
During the comprehensive design deployment of the engine assembly line, the large number and high complexity of design machines, as well as changes in the actual factory layout compared to the initial design drawings, presented challenges. The most significant difficulty was adjusting product sizes and models after finalizing the design.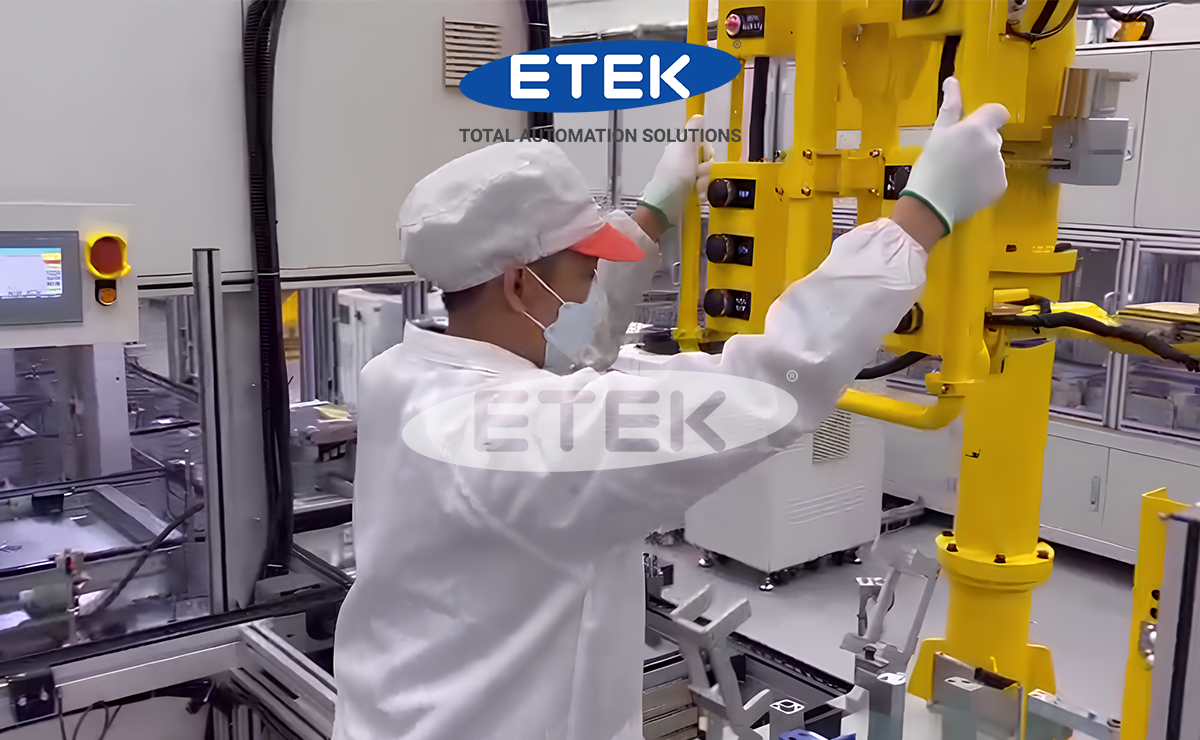
Building Success
Customer-Centric Approach
With the motto "The Customer is God," ETEK aims for customer satisfaction as the key to the success of every project. Despite facing challenges from design to problem-solving, installation, and commissioning, ETEK has earned satisfaction and trust from the engine assembly line through practical actions:- Meeting customer requirements from start to acceptance.
- Listening, understanding, and sharing challenges with customers.
- Supporting innovative design changes.
- Working overtime in three shifts.
- Developing contingency plans for supplies.
Key to Success
AUTOMATION- Automating the engine assembly line.
- Semi-automation of each machine module.
- Automatic expansion of the assembly line.
- Automated quality control.
- Systematic monitoring automation.